Como Realizar o Alinhamento de Turbina a Vapor com Precisão
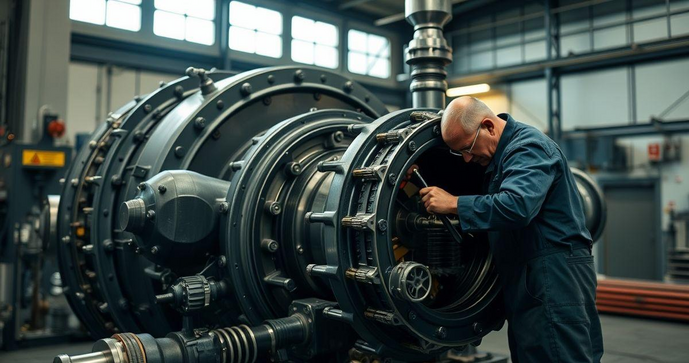
Por: Tiago - 19 de Abril de 2025
Importância do Alinhamento em Turbinas a Vapor
O alinhamento de turbina a vapor é fundamental para garantir o funcionamento eficaz e seguro deste tipo de equipamento. Um alinhamento inadequado pode resultar em uma série de consequências prejudiciais, incluindo vibrações excessivas e desgaste prematuro de componentes. Esses problemas não apenas afetam a eficiência da turbina, mas também podem levar a falhas catastróficas, que demandam intervenções dispendiosas e paradas inesperadas no sistema.
Além disso, um alinhamento correto contribui para a otimização do consumo energético. Quando a turbina está devidamente alinhada, a transferência de energia ocorre de forma mais eficiente, reduzindo o consumo de combustível e os custos operacionais. Esse benefício é especialmente relevante em um ambiente industrial onde a eficiência energética é uma prioridade cada vez maior.
Outro aspecto importante a ser considerado é o impacto na vida útil dos componentes da turbina. Um alinhamento preciso minimiza o esforço sobre os rolamentos e outras partes móveis, prolongando assim a durabilidade e a confiabilidade do equipamento. Com isso, investindo na manutenção adequada e no alinhamento regular das turbinas a vapor, as empresas podem não apenas garantir a continuidade das operações, mas também aumentar a segurança dos trabalhadores que operam esses sistemas complexos.
Nesse sentido, é evidente que o alinhamento de turbinas a vapor não deve ser subestimado. A prática regular de alinhamento não só preserva o investimento inicial feito no equipamento, mas também se traduz em ganhos financeiros e operacionais significativos ao longo do tempo.
Passo a Passo para Alinhar a Turbina Corretamente
Alinhar uma turbina a vapor corretamente é essencial para garantir seu funcionamento eficiente. A seguir, apresentamos um passo a passo para realizar esse alinhamento de forma eficaz:
1. Preparação e Inspeção Inicial: Antes de iniciar o processo de alinhamento, é fundamental realizar uma inspeção detalhada da turbina e de todos os elementos envolvidos, como o eixo e os suportes. Verifique se há desgastes visíveis e qualquer sinal de danos.
2. Desconectar a Turbina: Para evitar riscos durante o alinhamento, desconecte a turbina de outros componentes do sistema. Isso inclui a remoção de correias e desacoplar dispositivos elétricos que possam ser afetados durante o procedimento.
3. Utilizar Ferramentas de Alinhamento: Utilize ferramentas adequadas, como os alinhadores a laser ou sistemas de medição por tiras, que ajudam a identificar desvios e garantir uma medição precisa. A escolha da ferramenta poderá influenciar significativamente no resultado do alinhamento.
4. Medir o Desvio: Posicione as ferramentas nos eixos da turbina e registre as medições de desvio. É importante realizar medições em diferentes pontos ao longo do eixo para garantir uma avaliação completa.
5. Ajustes Necessários: Após obter as medições, é hora de realizar os ajustes necessários. Eleve ou abaixe a turbina conforme os resultados obtidos e certifique-se de que o nível esteja correto. O alinhamento pode requerer a colocação de calços ou a utilização de ferramentas específicas para ajustes finos.
6. Verificação de Repetibilidade: Após os ajustes, repita as medições para confirmar se o alinhamento foi corrigido. A precisão nas medições é crucial nesta etapa para garantir que a turbina esteja perfeitamente alinhada.
7. Fixação Final: Uma vez que a turbina esteja alinhada corretamente, fixe todos os componentes de forma segura. Certifique-se de que nada esteja solto, pois isso pode provocar problemas futuros em seu funcionamento.
8. Reanexar Componentes: Reconecte a turbina a todos os sistemas e componentes do seu entorno, garantindo que todas as conexões estejam firmes e seguras.
9. Teste de Funcionamento: Após completar todos os passos, realize um teste de funcionamento para verificar se a turbina opera suavemente e sem vibrações indesejadas. Isso garantirá que o sistema esteja pronto para operação normal.
Esses passos, quando seguidos com rigor e atenção aos detalhes, ajudam a garantir que a turbina a vapor funcione de forma eficaz e confiável, reduzindo o risco de falhas mecânicas e aumentando a eficiência geral do sistema.
Principais Ferramentas Necessárias para o Processo
A correta realização do alinhamento de turbinas a vapor exige não apenas conhecimento técnico, mas também o uso das ferramentas adequadas. A seguir, apresentamos as principais ferramentas necessárias para o processo:
1. Alinhadores a Laser: Um dos instrumentos mais precisos e modernos para o alinhamento de turbinas, os alinhadores a laser utilizam tecnologia de feixe de laser para medir desalinhamentos. Eles oferecem visualizações em tempo real e são fáceis de usar, garantindo um alinhamento eficiente.
2. Calibradores de Uso Geral: Ferramentas de calibração são essenciais para medir as distâncias e os ajustes necessários. Isso pode incluir calibres digitais ou mecânicos que ajudam a assegurar que as medidas sejam exatas antes de qualquer ajuste.
3. Níveis de Bolha: Um nível de bolha é crucial para garantir que a turbina e os componentes associados estejam em posição horizontal correta. Essa ferramenta é simples, mas extremamente eficaz para verificar ajustes de nível.
4. Micrômetros e Paquímetros: Essas ferramentas de medição são úteis para obter medidas precisas das partes do equipamento. Os micrômetros são usados para medidas mais finas, enquanto os paquímetros oferecem medições variadas, ajudando a identificar variações nos componentes.
5. Conjunto de Calços: Os calços ajustáveis são fundamentais para elevar ou abaixar partes da turbina durante o processo de alinhamento. Ter um conjunto de calços prontos e adequados facilita o ajuste de altura sem a necessidade de desmontar a turbina.
6. Torquímetro: Essa ferramenta é utilizada para garantir que os parafusos e fixações estejam tensionados com a força adequada, evitando danos por aperto excessivo ou folgas que possam comprometer o alinhamento.
7. Software de Alinhamento: Alguns sistemas podem integrar software especializado que auxilia no alinhamento e na análise dos dados coletados pelas ferramentas de medição. Esse tipo de software oferece relatórios detalhados e ajuda na identificação de padrões ou problemas recorrentes.
8. Câmeras de Inspeção: Em alguns casos, câmeras de inspeção podem ser utilizadas para visualizar áreas de difícil acesso, permitindo que os técnicos inspecionem as condições gerais do equipamento sem realizar desmontagens complexas.
Cada uma dessas ferramentas desempenha um papel significativo no processo de alinhamento de turbinas a vapor. O uso correto e a manutenção dessas ferramentas são fundamentais para garantir precisão e eficácia em cada tarefa realizada, contribuindo para o desempenho e a durabilidade da turbina nos sistemas de geração de energia.
Erros Comuns em Alinhamentos de Turbinas e Como Evitá-los
Alinhar turbinas a vapor é um procedimento delicado e, quando não executado corretamente, pode resultar em sérios problemas de funcionamento. Abaixo, estão alguns dos erros mais comuns cometidos durante o alinhamento e dicas sobre como evitá-los:
1. Medidas Inadequadas: Um dos erros mais frequentes é realizar medições imprecisas. Isso pode ocorrer devido ao uso de ferramentas inadequadas ou à falta de conhecimento técnico. Para evitar esse problema, sempre utilize ferramentas calibradas e de qualidade e verifique duas ou mais vezes as medições feitas.
2. Desconsiderar as Condições Ambientais: A temperatura e a umidade podem afetar as medições e o funcionamento da turbina. Os operadores devem sempre considerar as condições ambientais antes de realizar o alinhamento. Realizar o procedimento em um ambiente controlado é fundamental para garantir a precisão.
3. Não Verificar a Base de Montagem: Se a base da turbina não estiver nivelada ou estiver danificada, o alinhamento pode ser comprometido. É essencial inspecionar a base antes de iniciar o alinhamento e, se necessário, fazer reparos antes de proceder.
4. Uso Inadequado de Calços: Outra prática comum é a aplicação incorreta de calços durante o alinhamento. Isso pode levar a um desalinhamento ainda maior. Certifique-se de utilizar calços adequados e de ajustá-los de maneira uniforme para garantir que a turbina fique nivelada.
5. Não Considerar o Desgaste de Componentes: O desgaste acumulado em rolamentos e eixos pode afetar o alinhamento. Ignorar esse aspecto pode resultar em medições erradas. Portanto, é importante inspecionar todos os componentes antes de alinhar a turbina e substituir peças desgastadas conforme necessário.
6. Não Testar Após o Alinhamento: Após concluir o alinhamento, muitos técnicos não realizam testes para verificar se a turbina está funcionando adequadamente. Realizar um teste de funcionamento é essencial para confirmar que o alinhamento foi exitoso e para identificar quaisquer problemas iniciais que possam surgir.
7. Falta de Documentação: A falta de documentação durante o processo de alinhamento pode levar a erros na repetição do procedimento em futuras manutenções. É crucial manter um registro detalhado do processo, incluindo medições, ajustes e quaisquer problemas encontrados. Isso facilita o acompanhamento e a correção de problemas no futuro.
8. Ignorar a Programação do Motor: Para turbinas que possuem motores com sistemas de controle, a programação incorreta pode causar desalinhamentos e falhas. A verificação das configurações e o ajuste conforme as recomendações do fabricante são fundamentais para um alinhamento bem-sucedido.
Evitar esses erros comuns pode impactar significativamente a eficiência e a segurança das turbinas a vapor. Ao seguir as melhores práticas e realizar o processo com atenção e conhecimento, é possível assegurar um alinhamento eficaz e prolongar a vida útil do equipamento.
Impacto do Alinhamento na Eficiência Energética
O alinhamento adequado de turbinas a vapor desempenha um papel crucial na eficiência energética de sistemas de geração de energia. Um alinhamento preciso não apenas melhora o desempenho da turbina, mas também traz uma série de benefícios relacionados ao consumo de energia e à redução de custos operacionais. Aqui estão alguns dos principais impactos do alinhamento na eficiência energética:
1. Redução de Vibrações: Um alinhamento correto minimiza as vibrações dentro da turbina, que podem causar perda de eficiência e desgaste em componentes. Vibrações excessivas levam a um aumento no consumo de energia e à necessidade de manutenção mais frequente, impactando diretamente os custos operacionais.
2. Melhor Transferência de Energia: Quando a turbina está alinhada adequadamente, a transferência de energia entre os diferentes componentes do sistema é otimizada. Isso significa que uma maior parte da energia gerada é convertida em trabalho útil, aumentando a eficiência geral do sistema.
3. Menor Desgaste Mecânico: O desalinhamento causa um aumento no atrito e no desgaste mecânico dos componentes da turbina. Com o alinhamento adequado, as forças são distribuídas de maneira uniforme, reduzindo o atrito e prolongando a vida útil da turbina. Isso também resulta em menos interrupções de manutenção, economizando recursos a longo prazo.
4. Economia de Combustível: Em sistemas que utilizam combustíveis fósseis ou biocombustíveis, um alinhamento correto reduz a quantidade de combustível necessária para operar a turbina de maneira eficiente. Com uma melhor combustão e menos energia perdida em forma de calor, o uso de combustível se torna mais econômico.
5. Aumento na Capacidade de Geração: Com um alinhamento eficiente, a turbina pode operar em sua capacidade máxima sem as limitações impostas por problemas mecânicos. Essa capacidade de gerar mais energia contribui significativamente para a eficiência de todo o sistema, aumentando a produção energética total.
6. Sustentação do Desempenho ao Longo do Tempo: Turbinas que são regularmente alinhadas de maneira adequada tendem a manter seu desempenho ao longo dos anos. Isso se traduz em menor variação de eficiência, o que é vital em sistemas que dependem de produção energética constante e previsível.
7. Sensibilidade a Condições de Operação: A operação de turbinas desalinhadas pode ser mais sensível a mudanças nas condições ambientais e operacionais, como variações de temperatura e pressão. Quando alinhadas corretamente, as turbinas apresentam maior resiliência e adaptabilidade a essas variações, mantendo a eficiência em diferentes condições.
Em resumo, o impacto do alinhamento na eficiência energética de turbinas a vapor não pode ser subestimado. Investir em um alinhamento correto é uma estratégia que pode levar a economias significativas, menor impacto ambiental e uma operação mais estável e confiável.
Manutenção Preditiva e Alinhamento de Turbinas a Vapor
A manutenção preditiva é uma abordagem fundamental para a gestão eficaz de turbinas a vapor, permitindo que os operadores identifiquem e solucionem problemas antes que se tornem falhas significativas.
O alinhamento das turbinas desempenha um papel crucial nesse contexto, contribuindo para a eficiência e a longevidade do equipamento.
A seguir, são apresentados os principais aspectos da relação entre manutenção preditiva e alinhamento de turbinas a vapor:
1. Monitoramento Contínuo: A manutenção preditiva utiliza tecnologias de monitoramento contínuo, como sensores de vibração e temperatura, para coletar dados em tempo real. Esses dados ajudam a identificar desalinhamentos ou outras anomalias que possam afetar o desempenho da turbina, permitindo que intervenções sejam realizadas antes que o problema se agrave.
2. Análise de Tendências: Ao integrar análises de dados históricos e atuais, é possível identificar padrões e tendências que indicam quando um alinhamento pode ser necessário. Essa prática ajuda a programar manutenções de forma mais eficiente, minimizando o tempo de inatividade e reduzindo os custos associados.
3. Planejamento de Paradas Programadas: A manutenção preditiva permite que os operadores planejem paradas programadas para alinhamentos e outras manutenções, garantindo que a turbina opere nas condições ideais. Isso é especialmente importante em ambientes industriais onde a continuidade da operação é crucial para a produtividade.
4. Treinamento de Equipes: Implementar uma estratégia de manutenção preditiva envolve capacitar as equipes responsáveis pelo alinhamento e pela manutenção da turbina. Treinar trabalhadores para interpretar dados de monitoramento e realizar ajustes oportunos é essencial para garantir a eficiência e segurança da operação.
5. Otimização de Recursos: A manutenção preditiva, combinada com alinhamentos regulares, permite uma melhor alocação de recursos. Isso inclui a utilização de materiais e mão de obra, bem como a redução de desperdícios. A abordagem estratégica economiza tempo e dinheiro, mantendo a turbina em condições ideais de operação.
6. Feedback para Melhoria Contínua: A implementação de práticas de manutenção preditiva gera feedback que pode ser utilizado para aprimorar não apenas o processo de alinhamento, mas também outros aspectos da operação da turbina. A coleta de dados sobre alinhamentos anteriores e suas consequências ajuda as equipes a desenvolver técnicas de trabalho mais eficazes.
7. Desempenho Sustentável: Alinhamentos realizados dentro de um plano de manutenção preditiva contribuem para um desempenho sustentável das turbinas a vapor. Ao prevenir falhas e otimizar a eficiência, as empresas conseguem prolongar a vida útil dos equipamentos e reduzir o impacto ambiental associado à geração de energia.
Em resumo, a relação entre manutenção preditiva e alinhamento de turbinas a vapor é essencial para garantir que esses sistemas complexos operem de maneira eficiente e segura. Ao adotar práticas de monitoramento e alinhamento regulares, as organizações podem não apenas aumentar a confiabilidade e a eficiência de suas turbinas, mas também promover um ambiente operacional mais sustentável.
O alinhamento de turbinas a vapor é um fator crítico na operação eficiente e segura desses sistemas de geração de energia.
Ao seguir as melhores práticas de alinhamento, minimizar erros e integrar a manutenção preditiva, é possível garantir que as turbinas operem em máxima eficiência, reduzindo custos operacionais e prolongando a vida útil do equipamento.
A importância do alinhamento reflete-se diretamente na eficiência energética, na redução de vibrações e no menor desgaste dos componentes.
Investir em processos de alinhamento regulares, junto a um plano de manutenção bem estruturado, ajuda a assegurar que as turbinas a vapor ofereçam um desempenho confiável e sustentável ao longo do tempo.