Alinhamento de Turbinas: Tudo que Você Precisa Saber
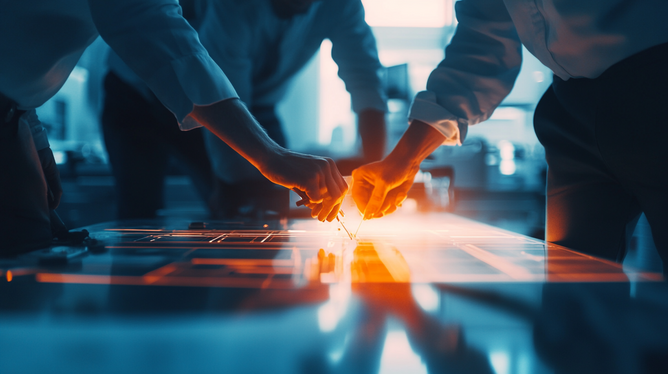
Por: Tiago - 10 de Dezembro de 2024
Alinhamento de turbinas é um aspecto crucial no funcionamento eficiente de sistemas industriais. A precisão nesse processo não apenas otimiza o desempenho, como também prolonga a vida útil dos equipamentos. Neste artigo, abordaremos o que é o alinhamento de turbinas, sua importância, os métodos utilizados e os sinais que indicam possíveis problemas. Continue lendo para entender como garantir que suas turbinas operem na melhor condição possível.
O que é Alinhamento de Turbinas
Alinhamento de turbinas refere-se ao processo de ajustar a posição de um eixo de turbina em relação aos componentes adjacentes, como geradores ou bombas. A precisão nesse alinhamento é fundamental para garantir que a turbina opere de forma eficiente, evitando desgaste irregular e danos aos equipamentos. Um alinhamento incorreto pode resultar em vibrações excessivas, aumento do consumo de energia e, em casos extremos, falhas catastróficas.
O alinhamento de turbinas é um componente essencial na manutenção preditiva e preventiva de sistemas mecânicos. Ele deve ser realizado com regularidade e, preferencialmente, sempre que uma manutenção significativa é realizada, como na troca de rolamentos ou quando novos equipamentos são instalados. O alinhamento correto garante que a energia gerada pela turbina seja transmitida de maneira eficiente para os componentes subsequentes, minimizando perdas operacionais.
Tipos de Alinhamento de Turbinas
Existem basicamente dois tipos de alinhamento de turbinas: o alinhamento estático e o alinhamento dinâmico. Cada um tem suas particularidades e métodos específicos de execução.
Alinhamento EstáticoO alinhamento estático envolve a verificação das posições dos componentes em repouso, sem a presença de movimento. Esse método é frequentemente aplicado durante processos de instalação ou manutenção. Os técnicos utilizam instrumentos de medição, como níveis e goniômetros, para determinar se os eixos estão na mesma linha axial. Qualquer desvio identificado deve ser corrigido ajustando os suportes ou bases onde as turbinas estão instaladas.
Alinhamento DinâmicoPor outro lado, o alinhamento dinâmico é realizado durante a operação dos equipamentos. Este método é mais complexo, pois envolve a análise das vibrações e do desempenho da turbina enquanto ela está em funcionamento. Sensores de vibração são utilizados para medir os níveis de desvio e, a partir disso, ajustes são realizados para corrigir a posição do eixo. O alinhamento dinâmico oferece uma visão mais precisa do desempenho em condições reais de operação.
Instrumentos Usados no Alinhamento de Turbinas
Para realizar o alinhamento de turbinas, diferentes tipos de instrumentos podem ser empregados. Cada um deles possui suas vantagens e desvantagens, dependendo das condições de operação e das necessidades específicas do sistema. Aqui estão alguns dos instrumentos mais comuns:
- Níveis de Bolha: Usados para medições simples, os níveis de bolha podem ajudar a determinar se a superfície de montagem está alinhada horizontalmente.
- Goniômetros: Esses dispositivos medem ângulos e são úteis durante o alinhamento estático.
- Sensores de Vibração: Essenciais para o alinhamento dinâmico, esses sensores ajudam a identificar padrões de vibração que indicam desalinhamento.
- Câmeras Termográficas: Utilizadas para monitoramento a distância, essas câmeras ajudam a identificar pontos quentes que podem sugerir problemas de alinhamento.
- Laser de Alinhamento: Este é um dos métodos mais precisos e modernos, utilizando laser para garantir o alinhamento exato de componentes rotativos.
Consequências do Alinhamento Incorreto
As falhas no alinhamento de turbinas podem resultar em diversas consequências negativas, afetando tanto o desempenho do equipamento quanto a segurança do sistema. Algumas das principais consequências incluem:
- Vibrações Excessivas: O desalinhamento provoca vibrações que podem se propagar para outros componentes, causando danos em longo prazo.
- Aumento do Desgaste: Componentes em desalinhamento tendem a se desgastar mais rapidamente, resultando na necessidade de manutenções mais frequentes.
- Perda de Eficiência: O consumo de energia aumenta quando as turbinas não estão corretamente alinhadas, diminuindo a eficiência geral do sistema.
- Quebras e Falhas Catastróficas: Em casos extremos, o desalinhamento pode levar a quebras, resultando em paradas inesperadas e custos de reparo elevados.
Boas Práticas para Alinhamento de Turbinas
Realizar o alinhamento de turbinas de maneira correta requer a aplicação de boas práticas e o uso de tecnologias adequadas. Aqui estão algumas dicas para garantir que o alinhamento seja realizado com precisão:
- Planejamento: Faça um planejamento detalhado da manutenção, incluindo a verificação do alinhamento como parte do processo.
- Treinamento da Equipe: Treine os membros da equipe para que compreendam a importância do alinhamento e saibam operar os instrumentos adequadamente.
- Utilização de Tecnologia: Invista em ferramentas de alinhamento moderno, como alinhadores a laser, para garantir maior precisão.
- Monitoramento Contínuo: Após o alinhamento, mantenha um plano de monitoramento regular para verificar se o alinhamento se mantém correto ao longo do tempo.
- Registro de Dados: Mantenha registros detalhados das medições e manutenções realizadas para análise futura e identificação de padrões de desgaste.
Considerações Finais sobre Alinhamento de Turbinas
O alinhamento de turbinas é um fator vital para o sucesso operacional em sistemas industriais. A realização adequada desse processo não apenas previne danos e falhas, mas também maximiza a eficiência e a vida útil dos equipamentos. Portanto, é essencial que os profissionais do setor compreendam a importância do alinhamento e implementem processos corretos para sua execução.
Com o uso de tecnologia adequada e a compreensão dos princípios envolvidos no alinhamento, as indústrias podem assegurar o funcionamento ideal de suas turbinas e evitar os custos dispendiosos associados a falhas operacionais. Investir tempo e recursos no alinhamento de turbinas é, sem dúvida, um passo necessário para qualquer operação industrial que dependa desse tipo de equipamento.
Importância do Alinhamento para o Desempenho
O alinhamento adequado de turbinas é uma condição fundamental para assegurar o desempenho eficiente de qualquer sistema que utilize essas máquinas. A importância do alinhamento vai além da simples colocação dos eixos em linha; ele envolve uma série de fatores que impactam diretamente na operação, na eficiência e na durabilidade do equipamento. Neste segmento, exploraremos de forma abrangente como o alinhamento correto contribui para o desempenho ideal de turbinas e quais são os benefícios associados a essa prática.
Efeito do Alinhamento no Desempenho da Turbina
Um alinhamento correto assegura que todas as partes móveis da turbina funcionem em harmonia, reduzindo o atrito e minimizando os riscos de desgastes prematuros.
Quando os eixos de uma turbina estão desalinhados, várias consequências adversas podem surgir:
- Aumento do Consumo de Energia: Um equipamento desalinhado requer mais energia para operar. Isso ocorre porque o sistema encontra resistência adicional durante o movimento. A eficiência energética de uma turbina pode ser reduzida em até 10% devido ao desalinhamento.
- Emissão de Vibrações: O desalinhamento gera vibrações excessivas. Essas vibrações não apenas afetam a turbina, mas também impactam negativamente os componentes adjacentes, podendo provocar falhas em outras partes da estrutura.
- Temperaturas Elevadas: A fricção gerada pelo desalinhamento pode resultar em aumento de temperatura, levando a um desgaste acentuado nos rolamentos e em outras peças móveis da turbina.
Impactos na Vida Útil do Equipamento
A vida útil de uma turbina pode ser significativamente reduzida se o alinhamento não for mantido corretamente. A manutenção regular do alinhamento pode prolongar a vida útil do equipamento de várias maneiras:
- Redução do Desgaste: Com o alinhamento adequado, o desgaste dos rolamentos e componentes mecânicos é minimizado, prolongando sua utilidade.
- Menos Paradas Não Programadas: O alinhamento regular diminui as chances de falhas inesperadas, permitindo que a turbina funcione ininterruptamente.
- Menor Necessidade de Manutenção: Enquanto turbinas desalinhadas podem exigir manutenções frequentes e custosas, um sistema alinhado funciona de forma mais suave e, portanto, precisa de intervenções menos frequentes.
Melhorias na Eficiência Operacional
Um dos benefícios mais significativos do alinhamento adequado é o aprimoramento da eficiência operacional. Quando a turbina está devidamente alinhada, vários aspectos do desempenho se beneficiam:
- Desempenho Otimizado: Um alinhamento preciso permite que a turbina opere no ponto mais eficiente, gerando a máxima produção de energia com o mínimo de consumo.
- Redução de Custos: A eficiência energética resultante do alinhamento correto reflete-se em menores custos operacionais. A economia em consumo pode ser substancial ao longo do tempo.
- Menos Perdas de Energia: O alinhamento adequado reduz as perdas mecânicas, garantindo que mais energia seja convertida em trabalho útil.
Confiabilidade do Sistema
A confiabilidade é outro fator crucial que se beneficia do gerenciamento eficaz do alinhamento de turbinas. Sistemas confiáveis impactam diretamente a continuidade operacional e a produtividade:
- Operação Sem Interrupções: Turbinas alinhadas são mais confiáveis, resultando em menos paradas inesperadas e manutenções não programadas.
- Aumento da Segurança: O alinhamento correto também previne situações perigosas, já que turbinas desalinhadas podem ocasionar falhas catastróficas de forma súbita, colocando em risco a segurança dos operadores.
- Maior Confiança no Processo: A certeza de que as turbinas estão funcionando corretamente permite que os operadores e gestores se concentrem em outras áreas de melhoria e expansão de negócios.
Impactos Ambientais Positivos
Além dos benefícios diretos para o desempenho e a eficiência, o alinhamento adequado de turbinas também pode ter implicações ambientais positivas:
- Menos Emissões: Em operações industriais, turbinas desalinhadas podem causar um aumento nas emissões de gases de efeito estufa, uma vez que funcionam de maneira ineficiente. Alinhar as turbinas promove uma operação mais limpa.
- Uso Racional dos Recursos: A eficiência energética decorrente de um bom alinhamento reduz a necessidade de recursos adicionais, como combustíveis, para operar os equipamentos.
- Menos Resíduos: A manutenção de uma operação eficiente também resulta em menos resíduos gerados ao longo do tempo, contribuindo para uma produção mais sustentável.
Desenvolvimento e Capacitação da Equipe
Realizar o alinhamento de turbinas de forma correta não é apenas uma questão técnica; também envolve o desenvolvimento de habilidades e competências da equipe de manutenção e operação:
- Treinamento em Práticas de Alinhamento: Proporcionar treinamento contínuo para a equipe garante que todos estejam atualizados sobre as melhores práticas de alinhamento, aumentando a eficácia do processo.
- Valorização do Profissional: Profissionais bem treinados e capacitados são mais valorizados no mercado. Investir no desenvolvimento da equipe não só promove desempenho, mas também contribui para a retenção de talentos.
- Cultura de Manutenção Proativa: Um foco constante no alinhamento e na manutenção proativa forma uma cultura organizacional voltada para a eficiência e a prevenção de falhas.
Conclusão sobre a Importância do Alinhamento
A correção e manutenção do alinhamento de turbinas revelam-se vitais não apenas para a performance mecânica, mas também para a integridade operacional e sustentabilidade de processos industriais. Este aspecto não pode ser negligenciado, pois suas implicações se estendem além do ambiente imediato da turbina, afetando toda a cadeia produtiva e operacional.
O alinhamento adequado é mais do que uma necessidade operacional; é uma estratégia que se traduz em eficiência, economia, segurança e confiabilidade. As indústrias que priorizam o alinhamento em sua rotina de manutenção estão investindo no futuro de suas operações, visando não apenas atender às demandas atuais, mas também se preparar para os desafios do amanhã.
Métodos Comuns de Alinhamento de Turbinas
O alinhamento de turbinas é uma prática essencial para garantir a eficiência e a durabilidade dos equipamentos. Existem diversos métodos utilizados para realizar esse alinhamento, cada um com suas vantagens e desvantagens. Neste artigo, exploraremos os métodos mais comuns de alinhamento de turbinas, suas características, aplicações e a importância de cada um deles no desempenho geral do sistema.
1. Alinhamento por Métodos Tradicionais
Os métodos tradicionais de alinhamento incluem técnicas manuais que têm sido utilizadas por muitos anos. Embora possam não ser tão precisos quanto as tecnologias modernas, ainda são amplamente utilizados por sua simplicidade e eficácia em diversas situações.
1.1 Nível de BolhaO uso do nível de bolha é uma técnica básica, mas eficaz, principalmente em alinhamentos estáticos. Este método envolve a utilização de um nível de bolha colocado sobre as superfícies de montagem das turbinas. Se o nível não estiver em posição horizontal, isso indica que os eixos estão desalinhados.
É importante observar que, embora fácil de usar, esse método pode ter limitações em termos de precisão, especialmente em sistemas complexos. A técnica é mais indicada para verificações iniciais ou para ajustes simples nas máquinas.
1.2 GoniômetroO goniômetro é um dispositivo que mede ângulos e pode ser utilizado para determinar se os eixos estão corretamente alinhados. Este método é mais preciso do que o uso do nível de bolha e é comum em situações onde a correção instantânea é necessária.
Para utilizar um goniômetro, é crucial que a superfície de montagem esteja bem nivelada. Ele pode ser usado em conjunto com outros métodos para fornecer um diagnóstico mais preciso do alinhamento da turbina.
2. Alinhamento com Laser
Nos últimos anos, o alinhamento a laser tornou-se o método preferido em muitas indústrias devido à sua precisão e eficiência. O uso desta tecnologia permite que os operadores realizem o alinhamento em um tempo significativamente menor, com resultados mais confiáveis.
2.1 Princípio de FuncionamentoO alinhamento a laser funciona ao projetar um feixe de luz laser ao longo do eixo da turbina. Equipamentos de detecção são usados para registrar a posição do eixo, permitindo que os operadores vejam instantaneamente se o alinhamento está adequado ou se ajustes são necessários.
Esse método é altamente recomendado para sistemas que exigem precisão, como turbinas de grande porte. Ele também pode ser aplicado em alinhamentos dinâmicos, onde a operação em movimento é monitorada.
2.2 Vantagens do Alinhamento a LaserAs principais vantagens deste método incluem:
- Alta Precisão: A tecnologia a laser permite medições extremamente precisas, minimizando o risco de erro humano.
- Rapidez na Execução: O tempo de alinhamento é significativamente reduzido, permitindo que as operações sejam retomadas mais rapidamente.
- Facilidade de Uso: Os sistemas modernos de alinhamento a laser são muitas vezes fáceis de operar e exigem menos tempo de treinamento.
3. Alinhamento Dinâmico
O alinhamento dinâmico é realizado enquanto a turbina está em funcionamento, permitindo que os operadores verifiquem o desempenho em condições reais de operação. Este método é especialmente útil para identificar problemas que podem não ser detectados durante alinhamentos estáticos.
3.1 Sensores de VibraçãoUma parte vital do alinhamento dinâmico é o uso de sensores de vibração. Esses dispositivos monitoram as vibrações do equipamento enquanto ele opera, detectando padrões que indicam desalinhamento.
Ao usar sensores de vibração, os operadores podem determinar rapidamente se o alinhamento está correto ou se ajustes precisam ser feitos. Este método é particularmente eficaz em ambientes industriais onde as turbinas estão sujeitas a variações de carga e velocidade.
3.2 Análise ModalA análise modal é uma técnica utilizada para realizar o alinhamento dinâmico de maneira avançada. Essa técnica envolve o estudo do comportamento dinâmico da turbina e a identificação de modos de vibração.
Por meio da análise modal, os engenheiros conseguem determinar as frequências críticas do sistema e evitar condições que possam levar a falhas. Isso é especialmente importante em turbinas que operam em altas velocidades.
4. Alinhamento com Software de Monitoramento de Condição
Atualmente, muitos sistemas automatizados incluem software de monitoramento de condição que facilita o alinhamento de turbinas. Esses softwares integram dados de múltiplas fontes, incluindo sensores de vibração, temperatura e pressão, para fornecer uma visão abrangente do estado do equipamento.
O alinhamento com software permite que as equipes de manutenção diagnostiquem problemas rapidamente e planejem intervenções com base em dados reais, minimizando o tempo de inatividade e os custos associados.
4.1 Análise PreditivaCom a análise preditiva, o software pode prever quando um problema de alinhamento pode ocorrer, permitindo que as equipes realizem manutenção preventiva. Essa abordagem proativa é uma tendência crescente nas indústrias modernas e pode resultar em economias significativas.
4.2 Relatórios AutomáticosAlém disso, o software pode gerar relatórios automáticos sobre o estado do alinhamento, ajudando a equipe de manutenção a tomar decisões informadas e a registrar atividades para futuras consultas. Essa documentação é essencial para a melhoria contínua e a conformidade com as normas de qualidade.
5. Dicas para Realizar Alinhamento Eficiente
Independente do método escolhido, algumas boas práticas são essenciais para garantir um alinhamento eficiente:
- Treinamento da Equipe: A equipe deve ser treinada nos métodos de alinhamento e nas ferramentas utilizadas para garantir uma execução adequada.
- Verificação Regular: O alinhamento deve ser verificado regularmente, especialmente em sistemas que operam em condições difíceis ou variáveis.
- Documentação: Manter um registro detalhado dos alinhamentos realizados e das condições do equipamento pode ajudar na identificação de tendências e problemas potenciais.
- Certificação de Equipamentos: As ferramentas usadas para alinhamento devem ser calibradas e em boas condições para garantir a precisão nas medições.
6. Conclusão
O alinhamento de turbinas é um aspecto fundamental da manutenção industrial que pode impactar drasticamente a eficiência, segurança e desempenho operacional. Compreender e aplicar os métodos comuns de alinhamento, desde técnicas tradicionais até tecnologias modernas, é essencial para qualquer equipe de manutenção. A escolha do método mais adequado depende das especificidades do sistema, do ambiente de operação e dos objetivos de desempenho. Ao manter uma abordagem proativa em relação ao alinhamento, as indústrias podem não apenas prolongar a vida útil das turbinas, mas também otimizar a produtividade e reduzir os custos operacionais.
Sinais de Problemas no Alinhamento de Turbinas
O alinhamento adequado de turbinas é crucial para o funcionamento eficiente de sistemas industriais. No entanto, mesmo as turbinas mais bem projetadas podem sofrer desalinhamentos ao longo do tempo devido a diversos fatores, como desgaste, vibração e condições operacionais. Identificar precocemente os sinais de problemas de alinhamento é fundamental para evitar danos maiores e custos dispendiosos de manutenção. Neste artigo, iremos explorar os principais sinais que indicam problemas no alinhamento de turbinas, de forma a ajudar os operadores e engenheiros a realizar intervenções proativas e eficazes.
1. Vibrações Excessivas
Um dos sinais mais comuns de problemas de alinhamento em turbinas é o aumento das vibrações. Turbinas desalinhadas podem gerar vibrações que excedem os níveis aceitáveis, podendo causar danos não apenas à própria turbina, mas também a outros componentes do sistema.
As vibrações podem ser detectadas através de:
- Monitores de vibração: Dispositivos eletrônicos que registram as vibrações em tempo real ajudam a identificar se estão acima dos valores normais.
- Observação visual: Em alguns casos, os operadores podem notar os efeitos das vibrações, como movimento excessivo ou ruídos incomuns, mesmo sem equipamentos de medição.
Vibrações são prejudiciais pois aumentam a fadiga dos componentes, levando a falhas mecânicas prematuras. Quando identificadas, é essencial realizar uma avaliação do alinhamento imediatamente.
2. Aumento da Temperatura
Outro sinal importante de problemas de alinhamento é o aumento na temperatura dos componentes da turbina. Quando os eixos não estão corretamente alinhados, o atrito entre as partes móveis aumenta, gerando calor excessivo.
Os operadores devem monitorar de perto:
- Rolamentos: Elevadas temperaturas em rolamentos de turbinas são um indicador claro de problemas de alinhamento.
- Eixos: A temperatura no eixo da turbina deve ser medida regularmente para identificar anormalidades.
Para evitar danos significativos devido ao superaquecimento, é fundamental realizar verificações regulares da temperatura e, se necessário, agir rapidamente para corrigir o desalinhamento.
3. Desgaste Irregular
O desalinhamento pode levar a um desgaste irregular nas peças móveis da turbina. Isso pode ocorrer em rolamentos, engrenagens e outros componentes, resultando em falhas prematuras. Para identificar o desgaste irregular, os operadores devem:
- Inspecionar visualmente: O exame atencioso dos componentes pode revelar sinais de desgaste anômalo, como marcas ou arranhões, que indicam problemas no alinhamento.
- Realizar testes de torque: Medir o torque necessário para girar eixos e outros componentes pode indicar a presença de atrito excessivo devido a desalinhamento.
O desgaste irregular é um sinal de alerta que deve ser tratado imediatamente, não apenas para evitar falhas inesperadas, mas também para garantir a longevidade do equipamento.
4. Ruídos Incomuns
Ruídos anormais são frequentemente um indicativo de problemas no alinhamento. Turbinas desalinhadas podem produzir sons estrondosos, rangidos ou vibrações que não são normais durante a operação. Os operadores devem prestar atenção especial aos seguintes pontos:
- Tipos de Ruídos: Determinar a origem dos ruídos pode ajudar a identificar se o problema está relacionado ao alinhamento, ao desgaste ou a outros fatores.
- Análise Auditiva: A formação de uma equipe de manutenção treinada para realizar análises auditivas pode ser valiosa na detecção antecipada de problemas.
Ruídos excessivos devem ser investigados prontamente, pois podem indicar falhas iminentes ou a necessidade de manutenção do equipamento.
5. Desempenho Reduzido
O desalinhamento de turbinas pode resultar em um desempenho reduzido, afetando a eficiência geral do sistema. Os sinais de desempenho ruim podem incluir:
- Baixa Produção de Energia: Turbinas desalinhadas podem gerar menos energia do que o esperado, o que pode ser observado através das medições de saída.
- Consumo Exagerado de Combustível: Se a turbina está trabalhando mais do que o necessário, isso pode indicar problemas de eficiência relacionados ao desalinhamento.
Os operadores devem estar atentos aos indicadores de desempenho e ajustar conforme necessário, realizando uma avaliação do alinhamento se a eficiência cair abaixo dos padrões normais.
6. Anomalias em Transmissões de Energia
Outra área que deve ser monitorada de perto é a transmissão de energia da turbina. Se a turbina estiver desalinhada, isso pode causar anomalias na transferência de energia para outros componentes do sistema. Algumas indicações incluem:
- Deslizamento de Correias: Em sistemas que utilizam correias, o desalinhamento pode causar deslizamento, resultando em perdas de potência.
- Danos ao Sistema de Transmissão: Componentes, como engrenagens, podem sofrer danos devido ao estresse adicional causado por um desalinhamento.
Detectar problemas na transmissão de energia requer monitoramento contínuo e verificação da integridade dos componentes ao longo do tempo.
7. Deslocamento Visível dos Componentes
Em alguns casos, pode ser possível visualizar deslocamento ou desalinhamento dos componentes. Isso pode ser demonstrado por:
- Deslocamento do Eixo: Um eixo que não está alinhado visualmente pode ser um sinal claro de que o alinhamento precisa ser corrigido.
- Não-conformidade em Posições de Montagem: Verificações visuais em suportes, calços e outros pontos de montagem podem evidenciar desalinhamentos.
Realizar inspeções visuais regulares é uma boa prática, pois pode ajudar a identificar indicadores físicos de problemas de alinhamento antes que se tornem sérios.
8. Informações de Monitoramento de Condição
Com o avanço da tecnologia, muitos sistemas de turbinas modernos estão equipados com tecnologia de monitoramento de condição que pode alertar automaticamente os operadores sobre potenciais problemas, incluindo desalinhamento. Esses sistemas analisam dados em tempo real e podem fornecer informações como:
- Alertas de Vibração: Se os níveis de vibração de um componente excederem limites predefinidos, um alerta é enviado automaticamente.
- Relatórios de Manutenção: Os softwares podem gerar relatórios detalhados sobre o estado do alinhamento e as condições operacionais.
A utilização de ferramentas de monitoramento de condição deve ser uma prioridade para equipes industriais que operam turbinas, pois ajuda a assegurar a detecção precoce de problemas.
Conclusão
Identificar os sinais de problemas no alinhamento de turbinas é essencial para garantir a continuidade operacional, eficiência e a longevidade do equipamento. Vibrações excessivas, aumento de temperatura, desgaste irregular, ruídos incomuns, desempenho reduzido, anomalias em transmissões de energia, deslocamento visível dos componentes e informações provenientes de sistemas de monitoramento são todos indicativos que não devem ser ignorados.
Manter um programa de manutenção regular, que inclua verificações e testes do alinhamento, pode significar a diferença entre o bom funcionamento e a falha do equipamento. Portanto, as equipes de operação e manutenção devem estar sempre atentas a esses sinais e prontas para agir a fim de garantir que suas turbinas continuem operando em condições ideais.
Em suma, o alinhamento de turbinas é uma prática indispensável para a eficiência e a confiabilidade de sistemas industriais. Identificar sinais de problemas no alinhamento, como vibrações excessivas, aumento de temperatura e desgaste irregular, é fundamental para prevenir falhas catastróficas e garantir a continuidade operacional. A implementação de métodos adequados de alinhamento, seja por técnicas tradicionais ou tecnologias avançadas, pode melhorar significativamente a performance das turbinas. Ao estar atento a esses sinais e manter um programa de manutenção regular, as indústrias podem maximizar a eficiência de seus equipamentos, reduzir custos operacionais e prolongar a vida útil das turbinas. Portanto, investir em práticas de alinhamento não é apenas uma questão de manutenção, mas um passo estratégico em direção à excelência operacional e à sustentabilidade industrial.