Alinhamento de Turbinas: Como Garantir Eficiência
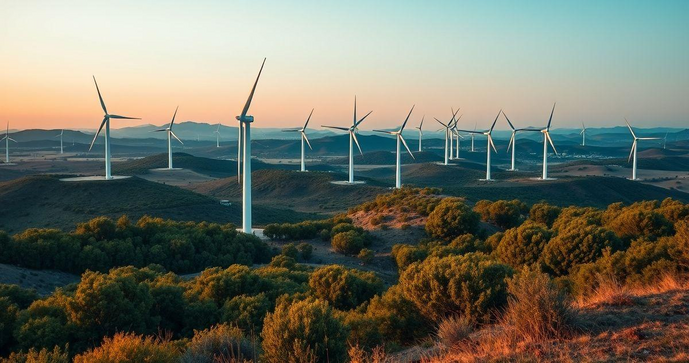
Por: Tiago - 16 de Março de 2025
O que é Alinhamento de Turbinas
O que é Alinhamento de Turbinas
O alinhamento de turbinas refere-se ao processo de garantir que as partes rotativas, como eixos e rolamentos, estejam devidamente alinhadas umas com as outras. Essa prática é essencial porque turbinas desalinhadas podem resultar em vibrações excessivas, desgaste acelerado das peças e até mesmo falhas catastróficas no equipamento.
Existem dois tipos principais de alinhamento: o alinhamento estático, que verifica a posição em repouso das partes, e o alinhamento dinâmico, que analisa o comportamento das turbinas em operação. O objetivo final é que a energia gerada seja utilizada da forma mais eficiente possível, evitando perdas que possam comprometer a performance do sistema.
O alinhamento é um processo que deve ser executado por profissionais qualificados, utilizando ferramentas adequadas, como alinhadores a laser ou calços de alinhamento. Ao seguir as diretrizes corretas para o alinhamento de turbinas, é possível maximizar a eficiência e a durabilidade de todo o sistema.
Importância do Alinhamento Correto
Importância do Alinhamento Correto
O alinhamento correto de turbinas é um aspecto crítico que impacta diretamente o desempenho e a longevidade do equipamento. Quando as turbinas estão devidamente alinhadas, há uma melhor distribuição das forças, o que reduz a ocorrência de vibrações e o desgaste excessivo dos componentes. Isso se traduz em menos paradas para manutenção e, consequentemente, maior disponibilidade de produção.
Além disso, um alinhamento adequado contribui para a eficiência operacional. Turbinas desalinhadas podem ter um maior consumo de energia, resultando em custos elevados. Através do alinhamento correto, é possível otimizar o uso de energia e minimizar o impacto ambiental.
Outros aspectos importantes incluem a segurança das operações. Turbinas desalinhadas são mais propensas a falhas mecânicas, que podem resultar em acidentes de trabalho. Assim, garantir que o alinhamento esteja sempre em dia é vital não apenas para as máquinas, mas também para a proteção da equipe envolvida nas operações.
Métodos de Alinhamento de Turbinas
Métodos de Alinhamento de Turbinas
Existem diversos métodos para realizar o alinhamento de turbinas, cada um adequado a diferentes situações e tipos de máquinas. Os métodos mais comuns incluem:
- Alinhamento a Laser: Este é um dos métodos mais precisos e modernos. Utiliza feixes de laser para medir o alinhamento em tempo real. É menos suscetível a interferências externas e oferece resultados rápidos e confiáveis.
- Alinhamento com Regra ou Goniômetro: Este método tradicional envolve a utilização de uma régua ou goniômetro para medir as distâncias entre os eixos. Embora menos preciso que o método a laser, pode ser eficaz em algumas situações e é mais acessível.
- Alinhamento por Calços: Utilizando calços ou shim, esse método envolve ajustes manuais nas bases da turbina para alinhar os eixos. É uma técnica simples, mas requer cuidado e habilidade para garantir resultados adequados.
- Alinhamento Dinâmico: Realizado enquanto a turbina está em operação, permite observar e ajustar o alinhamento levando em conta a vibração e o comportamento mecânico em tempo real. É fundamental para garantir que o alinhamento se mantenha durante todo o funcionamento.
Cada um desses métodos tem suas vantagens e desvantagens. A escolha do método adequado depende do tipo de turbina, das condições de operação e da disponibilidade de equipamentos de medição. Um alinhamento bem-sucedido não só melhora a eficiência, mas também prolonga a vida útil do equipamento.
Ferramentas Utilizadas no Alinhamento
Ferramentas Utilizadas no Alinhamento
Para realizar o alinhamento de turbinas de maneira eficaz, é essencial contar com as ferramentas adequadas. A seguir, destacamos algumas das principais ferramentas utilizadas nesse processo:
- Alinhar a Laser: Equipamentos de alinhamento a laser proporcionam medições precisas e rápidas. Eles são compostos por um transmissor e receptor que, ao serem instalados nos eixos, emitem um feixe de laser. Essa tecnologia permite detectar desalinhamentos com máxima precisão, facilitando ajustes e evitando erros.
- Niveladores: Niveladores são usados para assegurar que a turbina esteja na posição correta antes de iniciar o processo de alinhamento. São fundamentais para garantir que a superfície onde a turbina será instalada esteja perfeitamente nivelada, evitando problemas futuros.
- Calços e Shims: Utilizados para ajustar a altura e o alinhamento das máquinas, os calços e shims são colocados entre a base da turbina e o solo. A escolha do material e da espessura corretos é crucial para obter resultados satisfatórios.
- Rotômetros e Acelerômetros: Essas ferramentas são utilizadas para medir vibrações e determinar a saúde geral de uma turbina. O monitoramento das vibrações pode indicar desalinhamento e outros problemas mecânicos, permitindo intervenções precoces.
- Softwares de Alinhamento: Integrações tecnológicas que podem auxiliar no cálculo e análise do alinhamento a partir de dados coletados. Esses softwares oferecem relatórios e gráficos, tornando mais fácil a interpretação das medições e a realização de ajustes necessários.
A escolha das ferramentas deve ser feita com base na complexidade do equipamento, nas condições de operação e na experiência da equipe responsável pelo alinhamento. Usar as ferramentas corretas garante um resultado mais eficiente e prolonga a vida útil das turbinas.
Sinais de Desalinhamento em Turbinas
Sinais de Desalinhamento em Turbinas
Identificar sinais de desalinhamento em turbinas é crucial para garantir a eficiência e a longevidade do equipamento. Abaixo, listamos alguns dos principais indicadores que podem indicar que uma turbina está desalinhada:
- Vibrações Excessivas: Uma das principais consequências do desalinhamento é o aumento das vibrações. Se você notar vibrações anormais durante a operação da turbina, isso pode ser um sinal claro de que o alinhamento precisa ser revisado.
- Desgaste Irregular: O desgaste desigual nos componentes da turbina, como rolamentos e mancais, pode indicar problemas de alinhamento. Monitorar constantemente o estado das peças e procurar desgaste anormal é uma prática essencial.
- Ruídos Incomuns: Ruídos estranhos ou incomuns, como rangidos, batidas ou chiados, podem ser resultado de desalinhamento. Esses sons podem indicar que as partes estão colidindo de forma inadequada devido a um alinhamento incorreto.
- Temperaturas Elevadas: O aumento da temperatura em rolamentos e outros componentes pode ser um sinal de que a turbina não está devidamente alinhada. O atrito excessivo causado pelo desalinhamento gera calor, que pode levar a falhas prematuras.
- Desvios de Medidas: Ao realizar medições de alinhamento, se os resultados mostrarem desvios que ultrapassam os limites aceitáveis, isso é uma forte indicação de que o alinhamento precisa ser corrigido. Medidas regulares são essenciais para detectar problemas precocemente.
Reconhecer esses sinais de desalinhamento rapidamente pode evitar falhas graves e ajudar a manter a turbina funcionando de forma eficiente. A realização de manutenções regulares e inspeções detalhadas é fundamental para garantir que os problemas sejam resolvidos antes que se tornem mais sérios.
Manutenção Preventiva de Turbinas
Manutenção Preventiva de Turbinas
A manutenção preventiva de turbinas é uma prática essencial para garantir a operação eficiente e segura dos equipamentos. Este tipo de manutenção envolve uma série de atividades programadas que visam identificar e corrigir potenciais problemas antes que eles se tornem falhas significativas.
Aqui estão alguns aspectos importantes a considerar:
- Inspeções Regulares: Realizar inspeções frequentes nas turbinas é fundamental. Isso inclui verificar o alinhamento, a condição de rolamentos, as vibrações e outros parâmetros operacionais. Inspeções sistemáticas ajudam a detectar anomalias desde o início.
- Monitoramento de Vibrações: A instalação de sistemas de monitoramento de vibração pode fornecer dados em tempo real sobre o estado da turbina. Esse monitoramento permite identificar rapidamente qualquer alteração que possa indicar desalinhamento ou desgaste excessivo.
- Lubrificação Adequada: A lubrificação correta das peças móveis é vital para evitar o desgaste prematuro e reduzir o atrito. A falta de lubrificação pode levar a um aumento na temperatura e a falhas mecânicas.
- Treinamento da Equipe: Capacitar a equipe responsável pela operação e manutenção das turbinas é crucial. Um pessoal bem treinado pode identificar problemas rapidamente e agir de forma eficaz, minimizando os riscos.
- Documentação e Registro: Manter um registro detalhado de todas as atividades de manutenção e inspeção é essencial. Isso inclui datas de serviço, observações e análises de desempenho. A documentação ajuda a prever quando a manutenção será necessária e a avaliar a eficácia das intervenções realizadas.
Ao implementar uma estratégia de manutenção preventiva robusta, é possível aumentar a confiabilidade das turbinas, reduzir paradas inesperadas e, consequentemente, prolongar a vida útil do equipamento. A prevenção é sempre mais eficaz e econômica do que a correção de falhas tardias.
Conclusão
A manutenção adequada e o alinhamento de turbinas são elementos fundamentais para garantir a eficiência e a durabilidade dos sistemas. Ao compreender a importância do alinhamento correto, os métodos disponíveis, as ferramentas essenciais e os sinais de desalinhamento, podemos assegurar que as turbinas operem de forma otimizada e segura.
Além disso, a implementação de uma estratégia de manutenção preventiva pode evitar falhas críticas e reduzir os custos operacionais.
É vital que as empresas adotem uma abordagem proativa na manutenção de seus equipamentos. Isso não apenas melhora a performance, mas também garante a segurança dos operadores.
Portanto, mantenha-se atento aos sinais de desalinhamento e realize manutenções regulares para maximizar a eficácia da sua turbina.
Convidamos você a compartilhar suas experiências em manutenção de turbinas ou a entrar em contato conosco para discutir mais sobre como podemos ajudar a otimizar o desempenho do seu sistema. Como você está aplicando estas práticas na sua operação? Pense nisso e comece a implementar melhorias hoje mesmo!