Alinhamento de turbina a vapor: Guia Completo
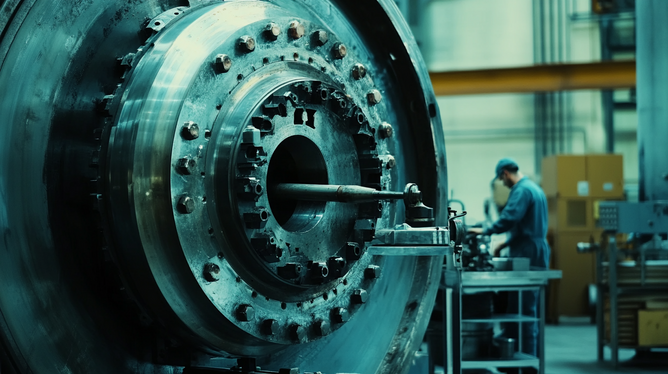
Por: Tiago - 10 de Dezembro de 2024
Alinhamento de turbina a vapor é um processo crucial para garantir a eficiência e o desempenho ideal de sistemas industriais. Neste artigo, vamos explorar a importância do alinhamento correto, as principais técnicas utilizadas, os sinais de que sua turbina pode estar desalinhada e os benefícios que isso traz para sua operação. Continue lendo para entender como esse procedimento pode impactar positivamente sua produtividade.
Importância do Alinhamento de Turbina a Vapor
O alinhamento de turbina a vapor é um aspecto fundamental na operação de sistemas industriais. Este processo não apenas assegura um desempenho eficiente, mas também contribui para a segurança e a longevidade dos equipamentos. Quando falamos sobre turbinas a vapor, estamos nos referindo a máquinas que desempenham um papel vital em diversas indústrias, como a geração de energia, refinarias e sistemas petroquímicos. Abaixo, veremos detalhadamente a importância do alinhamento de turbinas a vapor.
Eficiência Operacional
Um dos principais benefícios do alinhamento de turbina a vapor é o aumento da eficiência operacional. Quando turbinas estão desalinhadas, a energia gerada não é utilizada de forma ideal. O desalinhamento pode resultar em perda de eficiência, levando a um consumo maior de combustível e, consequentemente, a maiores custos operacionais. Além disso, uma turbina desalinhada pode provocar vibrações excessivas que, por sua vez, levam a um desgaste prematuro de componentes críticos.
Redução de Desgaste Mecânico
O desalinhamento causa forças adicionais que podem resultar em desgaste desnecessário de componentes mecânicos da turbina. Isso inclui rolamentos, selos, e até mesmo a própria estrutura de suporte da turbina. Quando a turbina está alinhada corretamente, as forças são distribuídas uniformemente, minimizando o estresse em todas as partes da máquina. Assim, o alinhamento não apenas prolonga a vida útil da turbina, mas também reduz a necessidade de manutenções frequentes e dispendiosas.
Segurança do Operacional
Além da eficiência e do desgaste mecânico, o alinhamento de turbina a vapor é vital para a segurança operacional. Equipamentos desalinhados podem falhar de maneira súbita, colocando em risco a vida dos operadores e causando danos significativos ao equipamento e à instalação. A manutenção regular do alinhamento serve como uma medida preventiva que ajuda a evitar falhas catastróficas e suas consequências. A segurança deve ser sempre uma prioridade em ambientes industriais, e um alinhamento adequado contribui significativamente para isso.
Minimizando Ruídos e Vibrações
Outra consequência do desalinhamento é a geração de ruídos e vibrações excessivas. Essas vibrações podem não apenas causar desconforto para os trabalhadores, mas também podem ser um sinal de que algo está errado na operação da turbina. Ruídos e vibrações anormais frequentemente precedem falhas no equipamento, então é crucial que as turbinas estejam em alinhamento para garantir uma operação tranquila. Um alinhamento adequado minimiza esses problemas, tornando o ambiente de trabalho mais seguro e agradavelmente operável.
Impacto no Desempenho da Turbina
O desempenho de uma turbina a vapor, em última análise, depende do seu alinhamento. Uma turbina desalinhada não consegue converter a energia do vapor em movimento mecânico da forma mais eficaz. Isso significa que mesmo que o sistema esteja produzido de forma eficiente, o desalinhamento pode ser um obstáculo para que essa eficiência se reflita na produção de energia ou em qualquer outra função que a turbina desempenhe. Por isso, a verificação e o ajuste do alinhamento devem ser parte integrante de qualquer programa de manutenção de turbinas a vapor.
Conformidade com Normas e Regulamentações
Em muitas indústrias, existem normas e regulamentações rigorosas que regem a operação de equipamentos industriais, incluindo turbinas a vapor. Alinhar esses dispositivos pode ser um requisito legal para garantir que a operação esteja conforme as normas de segurança e eficiência. Ignorar esse aspecto pode resultar em penalidades e em custos adicionais devido à necessidade de intervenções corretivas urgentes. Portanto, a conformidade com as normas não apenas evita problemas legais, mas também promove a reputação de uma empresa que prioriza a segurança e a eficiência.
Redução de Custos a Longo Prazo
Embora possa parecer um custo inicial significativo, investir em alinhamento de turbina a vapor é uma estratégia que reduz custos a longo prazo. Equipamentos bem alinhados exigem menos manutenção, têm uma vida útil maior e operam com maior eficiência. Isso se traduz em menos dinheiro gasto em reparos e substituições, além de uma redução nas contas de energia, já que a turbina consegue operar em seu potencial máximo. Assim, o alinhamento adequado não é apenas uma questão de manutenção, mas também uma estratégia financeira inteligente.
Facilidade na Manutenção Preemptiva
Um sistema de alinhamento bem instalado permite que os operadores monitorem a condição da turbina constantemente. Isso facilita a manutenção preemptiva, que é uma abordagem mais eficaz do que a manutenção reativa. Com a manutenção preemptiva, problemas menores podem ser identificados e corrigidos antes que se tornem falhas sérias. Isso não só melhora a eficiência operacional, mas também reforça a segurança do ambiente de trabalho.
Conclusão sobre a Importância do Alinhamento
O alinhamento de turbina a vapor é um processo essencial para garantir a eficiência, segurança e longevidade de um sistema industrial. Com todos os benefícios mencionados, fica claro que a indústria não pode se dar ao luxo de ignorar essa prática vital. Ao investir na manutenção adequada do alinhamento, as empresas podem assegurar não apenas a operacionalidade continuada de seus equipamentos, mas também um ambiente de trabalho mais seguro e produtivo.
Técnicas de Alinhamento de Turbina a Vapor
O alinhamento de turbina a vapor é uma tarefa crítica que deve ser realizada com precisão para garantir a eficiência e a segurança dos sistemas industriais. Existem várias técnicas de alinhamento que podem ser empregadas para assegurar que a turbina esteja corretamente alinhada com a sua base e com outros equipamentos conectados, como geradores e bombas. Este artigo abordará as principais técnicas de alinhamento, suas vantagens e desvantagens, e fornecerá orientações sobre como aplicá-las corretamente.
Alinhamento a Laser
O alinhamento a laser é uma das técnicas mais precisas e eficazes disponíveis para o alinhamento de turbinas a vapor. Neste método, um feixe de laser é projetado entre a turbina e o equipamento adjacente. Os dispositivos de medição posicionados no equipamento oposto detectam a luz do laser, permitindo que os operadores façam ajustes com base nas informações obtidas. Esta técnica é altamente precisa e pode identificar até mesmo pequenas desvios.
Vantagens: A precisão do alinhamento a laser é inigualável, e ele pode ser realizado rapidamente, economizando tempo de inatividade do equipamento. Além disso, este método reduz a necessidade de desmontagem de maquinaria, tornando o processo mais eficiente.
Desvantagens: O equipamento para alinhamento a laser pode ser caro, o que pode ser uma barreira para pequenas indústrias. Além disso, a técnica requer operadores treinados que saibam como usar os instrumentos adequadamente.
Alinhamento por Princípio de Coluna
Outra técnica popular para o alinhamento de turbinas a vapor é o alinhamento por princípio de coluna, que utiliza a gravidade para garantir que as partes da turbina estejam alinhadas. Este método envolve a instalação de colunas verticais que servem como referência para verificar o alinhamento da turbina em relação à base. A coluna é utilizada para observar as variações, garantindo que todo o conjunto esteja no nível correto.
Vantagens: Esta técnica é simples e não requer equipamentos sofisticados, o que a torna acessível para muitas empresas. Ela pode ser aplicada em situações onde as máquinas estão localizadas em ambientes adversos, onde o uso de dispositivos mais avançados seria problemático.
Desvantagens: O alinhamento por princípio de coluna é menos preciso do que o alinhamento a laser. Além disso, esse método pode ser mais demorado, especialmente em sistemas complexos com várias partes móveis.
Alinhamento por Mecanismo de Corda
O alinhamento por mecanismo de corda é uma técnica mais tradicional que usa cordas para medir o alinhamento entre a turbina e os equipamentos conectados. Neste método, as cordas são esticadas entre os pontos de referência e, em seguida, as distâncias são medidas para verificar se a turbina e o equipamento estão alinhados corretamente. Embora esse método possa ser um pouco rudimentar, ainda é usado em muitas instalações industriais.
Vantagens: Esta técnica é extremamente econômica e pode ser feita com ferramentas básicas disponíveis na maioria das oficinas. É uma opção viável quando não se tem acesso a instrumentos avançados.
Desvantagens: O alinhamento por mecanismo de corda é menos preciso e mais sujeito a erros humanos. Ele pode não ser apropriado para sistemas em que a precisão é fundamental, como turbinas a vapor de alta eficiência.
Jig de Alinhamento
Os jigs de alinhamento são ferramentas projetadas para ajudar na medição e ajuste do alinhamento entre a turbina e as máquinas adjacentes. Eles são especialmente úteis em instalações industriais em que as turbinas precisam ser repostas rapidamente. Um jig de alinhamento pode ser usado para alinhar a base e o eixo da turbina simultaneamente.
Vantagens: Os jigs são eficientes, pois podem ser preparados para uso em várias situações e aplicações. Eles ajudam a garantir que as medidas sejam repetíveis e confiáveis durante o processo de alinhamento.
Desvantagens: O uso de jigs pode requerer um investimento inicial em equipamentos, e a instalação dos jigs pode ser um processo que consome tempo. A eficácia do jig depende da habilidade do operador em utilizá-lo corretamente.
Testes de Vibração
Após o alinhamento da turbina, testes de vibração são essenciais para verificar se o alinhamento foi realizado corretamente. Os testes de vibração fornecem dados valiosos sobre a condição da turbina e ajudam a identificar problemas que podem ter sido negligenciados durante o processo de alinhamento. Sensores de vibração são posicionados em pontos estratégicos, e suas leituras são analisadas para identificar desvios e potenciais falhas.
Vantagens: Os testes de vibração são uma maneira eficaz de garantir a saúde geral da turbina e identificar problemas antes que se tornem críticos. Eles podem ser incorporados em rotinas de manutenção regulares.
Desvantagens: A instalação de sensores e a análise dos dados requer perícia técnica. Além disso, a interpretação dos resultados pode variar, dependendo da experiência do operador.
Cuidado e Manutenção Adequados
Independentemente da técnica de alinhamento escolhida, a manutenção regular e os cuidados são cruciais para garantir o desempenho a longo prazo. Isso inclui inspeções periódicas, verificação de montagens e parafusos, e atenção a sinais de desgaste nos componentes da turbina. Um programa de manutenção rigoroso pode ajudar a minimizar problemas de desalinhamento e aumentar a vida útil do sistema.
Treinamento e Qualificação de Funcionários
Uma parte importante do processo de alinhamento de turbinas a vapor é garantir que os funcionários envolvidos no processo sejam adequadamente treinados e qualificados. O conhecimento das diversas técnicas e a habilidade prática no uso de ferramentas são fundamentais para obter resultados eficazes. Com um treinamento adequado, as equipes podem melhorar a precisão do alinhamento e reduzir os erros associados ao processo.
Considerações Finais
O alinhamento de turbina a vapor é um aspecto crítico que deve ser tratado com cuidado e atenção. Cada técnica de alinhamento tem suas vantagens e desvantagens, e a escolha do método mais adequado depende das necessidades específicas da instalação e da equipe envolvida. Independentemente do método escolhido, garantir que a turbina esteja sempre alinhada adequadamente é fundamental para a eficiência, segurança e longevidade do equipamento industrial. Com o ambiente de trabalho seguro e eficiente, os benefícios operacionais e financeiros tornam-se uma realidade.
Sinais de Alinhamento Incorreto em Turbinas
O alinhamento correto das turbinas é fundamental para garantir o bom funcionamento de sistemas industriais que dependem de turbinas a vapor. Quando uma turbina não está alinhada corretamente, isso pode levar a uma série de problemas, desde a redução da eficiência até falhas catastróficas. É essencial que os operadores reconheçam os sinais de desalinhamento para que possam tomar medidas corretivas rapidamente. Neste artigo, discutiremos os principais sinais de alinhamento incorreto em turbinas e as implicações que esses problemas podem ter para a operação geral.
Vibrações Excessivas
Um dos sinais mais evidentes de que uma turbina pode estar desalinhada é a presença de vibrações excessivas. As vibrações são geralmente medidas em milímetros por segundo (mm/s) e podem ser detectadas por sensores de vibração instalados na turbina. Vibrações normais são esperadas em um sistema em funcionamento, mas quando as vibrações estão além dos limites aceitáveis, isso é um sinal de que algo pode estar errado.
Implicações: Vibrações excessivas não apenas indicam problemas de desalinhamento, mas também podem levar a danos mecânicos significativos, como desgaste prematuro de rolamentos, falhas em selos e até mesmo danos à estrutura da turbina. O monitoramento regular das vibrações pode ajudar a identificar problemas antes que se tornem críticos.
Ruídos Anormais
Outra indicação de desalinhamento em turbinas é a ocorrência de ruídos anormais. Normalmente, turbinas operam em uma faixa de ruído padrão. Se os operadores começarem a notar sons estranhos, como batidas, rangidos ou zumbidos, isso pode indicar um desalinhamento. Esses ruídos são frequentemente o resultado de partes da turbina que estão em contato inadequado entre si devido ao deslocamento de componentes internos.
Implicações: Ruídos anormais não são apenas irritantes; eles podem ser um precursor de problemas mais sérios. Se não tratados, esses sinais sonoros podem indicar que a turbina está prestes a falhar, resultando em paradas não planejadas e custos de reparo elevados.
Aquecimento Excessivo
O aquecimento excessivo das partes da turbina também pode ser um sinal de que a máquina não está devidamente alinhada. Quando uma turbina está desalinhada, isso pode resultar em pontos de atrito desnecessários entre os componentes, elevando a temperatura durante a operação. O monitoramento das temperaturas em pontos críticos é essencial para identificar esse problema.
Implicações: O calor excessivo não só diminui a eficiência da turbina, mas também pode levar ao desgaste de materiais e à falha prematura de componentes. Com o tempo, isso pode resultar em custos elevados para substituir peças danificadas ou até mesmo a necessidade de uma nova turbina.
Diminuição da Eficiência
Uma turbina desalinhada frequentemente apresenta uma diminuição na eficiência. Isso pode ser observado por meio de medições de desempenho, como pressão de saída e consumo de energia. Se a eficiência começar a cair sem uma explicação clara, o desalinhamento pode ser um dos culpados.
Implicações: A redução da eficiência não apenas afeta a produção, mas também aumenta os custos operacionais, uma vez que a turbina requer mais energia para realizar o mesmo trabalho. A perda de eficiência pode ser um sinal de que modificações devem ser feitas no alinhamento ou nas configurações da máquina.
Desgaste Prematuro de Componentes
Componentes internos da turbina, como rolamentos e engrenagens, sofrem desgaste considerável quando a turbina não está alinhada. O desalinhamento coloca cargas adicionais nestes componentes, o que pode resultar em falhas prematuras e a necessidade de trocas frequentes. Inspeções regulares devem ser realizadas para identificar sinais de desgaste.
Implicações: O desgaste prematuro dos componentes não só aumenta os custos de manutenção, mas também pode resultar em falhas inesperadas, prejudicando a operação e causando paradas indesejadas. Detectar e corrigir o desalinhamento pode ajudar a prolongar a vida útil dos componentes.
Deslocamento Visível
Um sinal óbvio de desalinhamento é o deslocamento visível entre a turbina e outros componentes conectados. Isso pode ser observado durante inspeções visuais, onde as falhas no alinhamento tornam-se evidentes. Linhas de referência podem ser utilizadas para verificar se a turbina está na posição correta em relação a outros equipamentos.
Implicações: O deslocamento visível é um alerta claro de que a correção é necessária. Não hesite em abordar o desalinhamento imediatamente, pois continuar operando com um equipamento visivelmente desalinhado pode resultar em danos mais sérios e problemas operacionais.
Quebras de Eixos
Quebras de eixos são uma das falhas mais graves que podem ocorrer devido ao desalinhamento. A sobrecarga nos eixos transporta tensões que, se não tratadas, podem levar a falhas catastróficas. Embora isso seja um sinal extremo de desalinhamento, é uma possibilidade real que deve ser considerada.
Implicações: As quebras de eixos não são apenas caras para reparar, mas também resultam em longos períodos de inatividade e perda de produção. Implementar um monitoramento preventivo pode ajudar a evitar que essa situação se desenvolva.
Manutenção e Monitoramento Contínuos
Reconhecer os sinais de desalinhamento é apenas o primeiro passo. A manutenção contínua e o monitoramento são fundamentais para garantir que as turbinas permaneçam operacionais e alinhadas. Realizar inspeções regulares e monitorar indicadores de desempenho, como vibrações e temperaturas, pode ajudar a detectar problemas antes que se tornem sérios.
Implicações: Investir em manutenção e monitoramento pode resultar em economias significativas a longo prazo. A proatividade na manutenção ajuda a evitar falhas inesperadas e pode prolongar a vida útil dos componentes da turbina.
Capacitação da Equipe
A capacitação dos operadores e da equipe de manutenção é crucial. Eles devem ser treinados para reconhecer os sinais de desalinhamento e entender como implementá-los de maneira eficaz. Aprofundar o conhecimento sobre os equipamentos e as técnicas de alinhamento pode ser um diferencial para as operações.
Implicações: Uma equipe bem treinada e informada será mais capaz de detectar problemas precocemente e implementar soluções adequadas. A melhoria contínua das habilidades da equipe ajuda a promover uma cultura de segurança e eficiência na operação das turbinas.
Conclusão sobre Sinais de Alinhamento Incorreto
Reconhecer os sinais de alinhamento incorreto em turbinas é fundamental para a manutenção e longevidade dos equipamentos. Desde vibrações excessivas e ruídos anormais até desgaste prematuro e quebras de eixos, a identificação desses sinais pode evitar problemas graves e custos elevados. Implementar um sistema de monitoramento eficiente e capacitar a equipe para agir rapidamente diante desses sinais é uma prática recomendada para operações de turbinas a vapor seguras e eficazes.
Benefícios do Alinhamento de Turbina a Vapor
O alinhamento adequado de turbinas a vapor é um aspecto crucial na operação de sistemas industriais. Este processo não apenas assegura a eficiência e a segurança das máquinas, mas também contribui para a sustentabilidade e rentabilidade das operações. Neste artigo, discutiremos os principais benefícios do alinhamento de turbina a vapor, oferecendo insights sobre como essa prática pode impactar positivamente sua operação.
Melhoria na Eficiência Energética
Um dos principais benefícios do alinhamento de turbinas a vapor é a melhoria na eficiência energética. Quando uma turbina está corretamente alinhada, ela pode converter a energia do vapor em energia mecânica eficazmente. O desalinhamento, por outro lado, causa perdas significativas de energia, obrigando a turbina a trabalhar mais para produzir a mesma quantidade de saída.
Implicações: Com um alinhamento correto, a turbina opera em sua eficiência máxima, permitindo que menos combustível seja consumido. Isso não apenas reduz os custos operacionais, como também diminui a pegada de carbono da instalação, tornando-a mais sustentável.
Redução de Desgaste e Manutenção
Quando as turbinas estão corretamente alinhadas, a carga é distribuída uniformemente entre todos os componentes. Isso reduz o desgaste mecânico em partes críticas, como rolamentos e engrenagens, que são frequentemente afetados pelo desalinhamento.
Implicações: A diminuição do desgaste resulta em menos paradas para manutenção, o que economiza tempo e recursos. Além disso, a vida útil dos componentes é prolongada, resultando em menos despesas com substituições de peças e menos desperdício de materiais.
Segurança Aumentada
A segurança é uma das prioridades mais significativas em qualquer operação industrial. O desalinhamento pode resultar em falhas catastróficas e acidentes que comprometem a segurança dos operadores e a integridade da instalação. A prática regular do alinhamento de turbinas a vapor contribui para um ambiente de trabalho mais seguro.
Implicações: Reduzir o risco de falhas inesperadas promove um ambiente de trabalho mais seguro. Isso não só protege a vida dos operadores, mas também minimiza a possibilidade de danos ao equipamento e a necessidade de paradas não planejadas.
Menos Vibrações e Ruídos
Um alinhamento correto resulta em uma operação mais suave e silenciosa, com menos vibrações e ruídos anormais. Vibrações excessivas e ruídos não apenas indicam problemas no equipamento, mas também podem causar desconforto e distração para os operadores.
Implicações: Mantenha um ambiente de trabalho mais confortável e seguro reduzindo o ruído e as vibrações. Isso pode aumentar a moral da equipe e melhorar a produtividade, permitindo que os operadores se concentrem em suas tarefas sem distrações significativas.
Melhor Desempenho Geral
O alinhamento adequado de turbinas a vapor resulta em um desempenho geral aprimorado. Isso se reflete em uma operação mais eficiente, com menos interrupções e um melhor controle sobre os processos produtivos. Turbinas alinhadas corretamente mostram um desempenho confiável em uma variedade de condições operacionais.
Implicações: Um melhor desempenho geral aumenta a produtividade e a eficiência do sistema, permitindo que as empresas atendam a demandas de produção de maneira mais eficaz. Além disso, um desempenho aprimorado pode levar a melhorias na qualidade do produto final.
Redução de Custos Operacionais
Todos os benefícios mencionados, desde a maior eficiência energética até a redução da necessidade de manutenção, levam à redução geral dos custos operacionais. A economia gerada pelo alinhamento adequado pode ser significativamente notável ao longo do tempo.
Implicações: Esses custos reduzidos podem ser reinvestidos na empresa, permitindo que os recursos sejam direcionados para áreas que precisam de mais atenção, inovação ou expansão. A eficiência financeira é crucial em um mercado competitivo, e o alinhamento adequado pode ser uma parte importante dessa estratégia.
Prolongamento da Vida Útil do Equipamento
O alinhamento regular de turbinas a vapor pode resultar em um prolongamento da vida útil do equipamento. Quando as turbinas estão alinhadas corretamente, o estresse sobre os componentes diminui, permitindo que eles operem em condições ideais por mais tempo.
Implicações: O prolongamento da vida útil do equipamento significa menos necessidade de substituições e uma possível redução no capital necessário para manutenção e aquisições. Isso representa uma economia relevante que diretamente impacta o balanço financeiro da empresa.
Conformidade com Normas e Regulamentações
Manter o alinhamento correto de turbinas a vapor também ajuda a garantir que a operação esteja de acordo com normas e regulamentações de segurança e desempenho. As indústrias muitas vezes precisam seguir diretrizes rigorosas para garantir a segurança e a eficiência.
Implicações: A conformidade com as normas não apenas evita multas e penalidades, mas também promove uma boa imagem da empresa no mercado. A reputação de uma instalação que prioriza a segurança e a eficiência é um ativo valioso, especialmente em indústrias regulamentadas.
Facilidade na Identificação de Problemas
Turbinas alinhadas corretamente facilitam a identificação de outros problemas que podem surgir durante a operação. Quando as leituras de vibração e desempenho estão dentro das faixas normais, fica mais fácil detectar anomalias que podem indicar falhas em outros componentes do sistema.
Implicações: Um sistema de monitoramento eficaz minimiza o tempo de inatividade ao permitir que a equipe identifique e resolva problemas antes que eles se tornem críticos. Isso garante uma operação mais confiável e contínua, aumentando a eficiência geral do sistema.
Contribuição para a Sustentabilidade
O alinhamento eficaz de turbinas a vapor não é apenas uma questão de eficiência e segurança, mas também está ligado à sustentabilidade. Turbinas bem alinhadas consomem menos combustíveis fósseis e geram menos emissões, contribuindo para um ambiente mais verde.
Implicações: Com um foco crescente na sustentabilidade das operações, garantir que suas turbinas estejam corretamente alinhadas demonstra um compromisso com a responsabilidade ambiental. Isso pode melhorar a reputação da empresa entre clientes e fornecedores que priorizam sustentação.
Capacitação e Conhecimento da Equipe
Investir no alinhamento de turbinas a vapor também leva a oportunidade de capacitar a equipe envolvida na manutenção e operação. O conhecimento adquirido sobre a importância do alinhamento e as técnicas adequadas podem melhorar a competência geral da equipe.
Implicações: Uma equipe bem treinada e informada promove um ambiente de trabalho que valoriza a melhoria contínua e a segurança. Isso contribui para um aumento na moral e motivação dos funcionários, resultando em uma operação de maior sucesso.
Conclusão sobre os Benefícios do Alinhamento
O alinhamento de turbinas a vapor oferece uma ampla gama de benefícios que vão além da simples correção de falhas mecânicas. Desde a melhoria da eficiência energética até a redução dos custos operacionais, cada um desses benefícios desempenha um papel importante no funcionamento geral da empresa. Investir no alinhamento adequado não é apenas uma prática recomendada, mas uma estratégia que pode levar a um sucesso duradouro no ambiente industrial atual.
Concluindo, o alinhamento de turbina a vapor é uma prática fundamental que não deve ser negligenciada em qualquer operação industrial. Ao garantir o alinhamento correto, as empresas não apenas aumentam a eficiência energética e reduzem custos operacionais, mas também promovem a segurança, prolongam a vida útil dos equipamentos e contribuem para um ambiente de trabalho mais sustentável. Compreender as técnicas de alinhamento, reconhecer os sinais de desalinhamento e perceber os benefícios dessa prática são passos essenciais para otimizar a operação. Ao investir na manutenção adequada do alinhamento de turbinas, as organizações podem assegurar uma performance confiável e contínua, permitindo que alcancem seus objetivos produtivos de forma eficaz e responsável.