Alinhamento de Redutores: Importância e Melhores Práticas
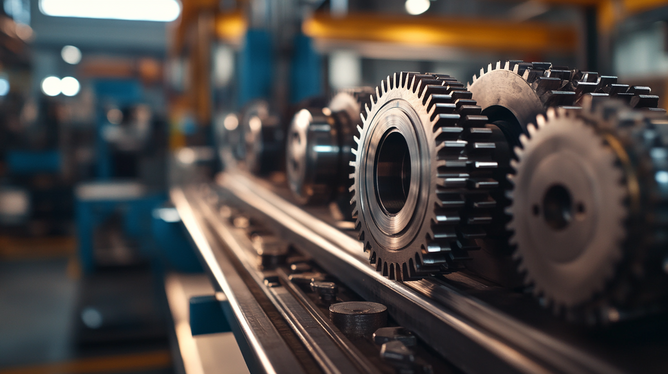
Por: Tiago - 24 de Dezembro de 2024
Alinhamento de redutores é um fator crucial para o bom funcionamento de equipamentos industriais. Quando realizado de maneira inadequada, pode resultar em desgaste excessivo, aumento de custos e diminuição da eficiência. Neste artigo, vamos explorar a importância do alinhamento de redutores, as melhores técnicas a serem utilizadas e os erros comuns a serem evitados. Continue lendo para descobrir como otimizar o desempenho da sua maquinaria por meio de um alinhamento eficaz.
Importância do Alinhamento de Redutores
O alinhamento de redutores desempenha um papel fundamental em diversas indústrias, pois está diretamente relacionado à eficiência e à durabilidade dos equipamentos. Um redutor mal alinhado pode gerar vibrações excessivas, desgastes prematuros e falhas mecânicas, resultando em paradas não programadas que podem afetar toda a linha de produção.
O redutor de velocidade é responsável por reduzir a rotação de um motor e amplificar o torque, garantindo que a máquina opere em sua faixa ideal. Para que esse processo ocorra de maneira eficiente, é vital que o redutor esteja alinhado corretamente com o motor e outros componentes do sistema. O alinhamento adequado elimina forças desnecessárias que podem comprometer a integridade dos equipamentos.
Uma das principais consequências de um alinhamento inadequado é o aumento do consumo de energia. Quando os componentes não estão alinhados, o motor trabalha mais para superar a resistência adicional criada por essas forças desiguais. Isso pode resultar em contas de energia mais altas e, em última análise, em um custo operacional maior.
Consequências de um Alinhamento Incorreto
As consequências de uma falha no alinhamento de redutores podem ser severas. Uma das consequências mais imediatas é o aumento das vibrações. Essas vibrações não apenas afetam o desempenho do redutor, mas também podem se propagar através das estruturas das máquinas, causando danos adicionais a outros componentes.
Além disso, um redutor desalineado pode levar ao aquecimento excessivo do motor e do redutor em si. O calor gerado pelo atrito adicional pode resultar em falhas nas partes internas do redutor, como os rolamentos, engrenagens e eixos. Isso pode acarretar em custos elevados de manutenção, além de diminuir a vida útil dos componentes.
Outro aspecto a ser considerado é a segurança. Equipamentos com alinhamento incorreto podem representar riscos para os operadores e para as instalações. Um redutor que falha durante a operação pode levar a acidentes graves, resultando em lesões ou até mesmo fatalidades.
Benefícios do Alinhamento Adequado
Agora que abordamos as consequências de um alinhamento inadequado, é importante destacar os benefícios do alinhamento correto dos redutores. Um dos principais benefícios é a melhoria na eficiência operacional. Equipamentos que estão alinhados corretamente consomem menos energia, o que resulta em uma redução significativa nos custos operacionais.
A durabilidade dos equipamentos também aumenta quando o alinhamento é realizado de forma adequada. O uso de componentes alinhados corretamente reduz o desgaste e a fricção, prolongando a vida útil tanto do redutor como do motor. Isso não apenas economiza recursos financeiros, mas também minimiza o impacto ambiental, pois menos resíduos são gerados durante o ciclo de vida do equipamento.
Outro benefício crítico é a redução das paradas não planejadas. Equipamentos que operam sem problemas de alinhamento tendem a ter uma taxa de disponibilidade mais alta, permitindo uma produção contínua e eficaz. Isso é especialmente importante em indústrias onde o tempo de inatividade pode resultar em perda de receita significativa.
Técnicas de Alinhamento
Existem várias técnicas que podem ser empregadas para garantir que o alinhamento dos redutores seja realizado de forma eficaz. Algumas das técnicas mais comuns incluem o uso de alinhadores a laser, alinhadores mecânicos e métodos de alinhamento visual. Cada uma dessas técnicas tem suas vantagens e desvantagens, dependendo do tipo de equipamento e da situação em que estão sendo utilizados.
O alinhamento a laser é uma das técnicas mais precisas e rápidas, permitindo que os operadores verifiquem o alinhamento em tempo real. Essa tecnologia facilita a identificação de desalinhamentos em questão de minutos, economizando tempo e recursos.
Os alinhadores mecânicos, por outro lado, são mais tradicionais e costumam ser mais acessíveis. Embora possam exigir mais tempo e esforço para serem empregados, eles ainda são eficazes na realização de alinhamentos precisos.
O alinhamento visual, embora menos convencional, pode ser útil em determinadas situações. Ele envolve a inspeção direta dos componentes e o ajuste manual até que o alinhamento pareça correto. Essa técnica é mais dependente da experiência do operador e pode resultar em medições menos precisas.
Manutenção e Monitoramento
Um alinhamento correto não é uma solução única. É essencial implementar um programa contínuo de manutenção e monitoramento para garantir que os redutores se mantenham alinhados ao longo de sua vida útil. O monitoramento regular permite que os operadores identifiquem rapidamente qualquer desvio no alinhamento e realizem ajustes antes que o problema se torne grave.
Além disso, a realização de inspeções periódicas, como a verificação das condições dos rolamentos e engrenagens, pode ajudar a prevenir problemas relacionados ao alinhamento. A manutenção preditiva, que utiliza técnicas de monitoramento para prever falhas, pode aumentar ainda mais a eficácia do alinhamento e da operação dos equipamentos.
Conscientização e Treinamento
Uma das chaves para garantir a importância do alinhamento de redutores é a conscientização dos operadores e da equipe de manutenção. O treinamento em técnicas de alinhamento e compreensão do impacto do desalinhamento devem ser incorporados ao programa de capacitação das equipes.
Promover uma cultura de manutenção proativa dentro da empresa pode ajudar a reduzir os custos associados a paradas não planejadas e falhas mecânicas. Quando todos na organização estão conscientes da importância do alinhamento, os resultados tendem a ser significativamente melhores.
Em resumo, o alinhamento de redutores não deve ser visto apenas como uma tarefa a ser cumprida, mas sim como um aspecto vital para a eficiência e a segurança operacional. Implementar práticas corretas de alinhamento pode resultar em melhorias significativas na performance dos equipamentos, além de contribuir para uma operação mais segura e econômica.
Investir no alinhamento adequado de redutores é investir em um futuro mais sustentável e produtivo para sua empresa. A atenção a esse detalhe pode fazer toda a diferença na continuidade dos processos e na saúde financeira do negócio.
Técnicas de Alinhamento de Redutores
O alinhamento de redutores é uma prática essencial para garantir a eficiência e durabilidade de equipamentos industriais. Um redutor bem alinhado não só melhora o desempenho do sistema, mas também reduz o desgaste e aumenta a vida útil dos componentes. Neste artigo, iremos explorar as principais técnicas de alinhamento de redutores, sua aplicabilidade, vantagens e desvantagens, além das melhores práticas para a implementação dessas técnicas.
1. Alinhamento Visual
O alinhamento visual é a técnica mais simples e tradicional, utilizada principalmente em situações onde não são necessários equipamentos sofisticados. Essa técnica envolve a inspeção visual dos eixos e a comparação da sua posição uns em relação aos outros.
Para realizar o alinhamento visual, os operadores devem:
- Desligar a máquina e garantir que não haja tensão nos eixos;
- Utilizar um nível de bolha ou régua para verificar se os eixos estão na mesma linha;
- Fazer ajustes nos suportes de montagem, conforme necessário, para alinhar os eixos.
Essa técnica é mais adequada para máquinas simples com um pequeno número de componentes. No entanto, a desvantagem do alinhamento visual é a dificuldade em obter medições precisas, especialmente em aplicações de alta velocidade e torque.
2. Alinhamento Mecânico
Esta técnica utiliza dispositivos mecânicos de alinhamento, como punções e alinhadores manuais. O alinhamento mecânico melhora a precisão em comparação ao alinhamento visual, permitindo ajustes mais precisos. Os passos para o alinhamento mecânico incluem:
- Desmontar os componentes e limpar as superfícies de contato;
- Colocar o alinhador mecânico entre os eixos;
- Ajustar os eixos até que o alinhador indique que eles estão alinhados corretamente.
O alinhamento mecânico é uma alternativa acessível e eficaz, especialmente em indústrias que não possuem acesso a tecnologia avançada. No entanto, ainda requer uma considerável habilidade do operador para garantir resultados precisos.
3. Alinhamento a Laser
O alinhamento a laser é uma das técnicas mais modernas e precisas para garantir o alinhamento correto de redutores. Essa técnica utiliza feixes de laser e dispositivos de medição para determinar a posição exata dos eixos, permitindo correções em tempo real.
Para realizar o alinhamento a laser, os passos incluem:
- Instalar o transmissor de laser em um dos eixos;
- Posicionar o receptor de laser no eixo oposto;
- Iniciar o sistema para medir a desvio entre os eixos;
- Ajustar a posição dos eixos com base nas medições indicadas pelo equipamento.
Os principais benefícios do alinhamento a laser incluem:
- Alta precisão nas medições;
- Tempo de configuração reduzido;
- Capacidade de armazenamento e registro das medições para futuras análises.
No entanto, o equipamento de alinhamento a laser pode ser mais caro e requer treinamento especializado para operação e interpretação dos resultados.
4. Alinhamento com Transferência de Carga
O alinhamento com transferência de carga é uma técnica menos comum, mas muito eficaz. Ela utiliza sensores de pressão e dispositivos de medição para avaliar a distribuição de carga nos eixos durante a operação. Esses dados ajudam a identificar desequilíbrios que podem indicar desalinhamento.
Os passos para implementar essa técnica envolvem:
- Instalar sensores de pressão nos suportes do redutor;
- Monitorar a carga durante a operação para identificar pontos de estresse;
- Ajustar o alinhamento com base nas medições de carga.
Essa técnica permite que os operadores ajustem os eixos sob condições de carga real, proporcionando uma visão mais precisa dos requisitos de alinhamento. Contudo, requer um entendimento refinado dos dados de pressão e pode ser mais complexa de implementar.
5. Importância da Prevenção e Manutenção
Independentemente da técnica escolhida, a prevenção e a manutenção contínua desempenham um papel crucial no sucesso do alinhamento de redutores. Para assegurar que o alinhamento se mantenha eficiente, algumas práticas recomendadas incluem:
- Realizar inspeções regulares para identificar sinais de desalinhamento, como vibrações e ruídos anormais;
- Implementar um cronograma de manutenção preditiva que inclua verificações de alinhamento em intervalos regulares;
- Treinar a equipe de manutenção e operadores nas melhores práticas de alinhamento e manutenção.
6. Adoção de Tecnologias Avançadas
A evolução da tecnologia tem trazido novos métodos e ferramentas para a medição e monitoramento do alinhamento de redutores. Muitas empresas têm adotado sistemas de monitoramento em tempo real que utilizam sensores e software avançado para detectar variações de alinhamento instantaneamente. Esses sistemas proporcionam vantagens como:
- Detecção precoce de problemas antes que se tornem críticos;
- Relatórios detalhados que ajudam na tomada de decisão;
- Integração com sistemas de gerenciamento de manutenção.
Essas tecnologias não substituem as práticas tradicionais, mas complementam os métodos existentes, garantindo que o alinhamento de redutores seja tratado de forma abrangente e eficaz.
7. Considerações Finais sobre Técnicas de Alinhamento
A escolha da técnica de alinhamento de redutores deve considerar fatores como o tipo de equipamento, o ambiente operacional e o nível de precisão necessário. A implementação correta de um método de alinhamento não só economiza recursos, mas também melhora a produtividade e a segurança dos trabalhadores.
Além disso, é vital que as empresas invistam em treinamento e desenvolvimento contínuos para suas equipes. O conhecimento e a experiência dos operadores e pessoal de manutenção são fundamentais para garantir que as técnicas de alinhamento sejam executadas de maneira eficiente e eficaz.
Por fim, a prática do alinhamento de redutores deve estar inserida dentro de um contexto de melhoria contínua e inovação. A adoção de novas tecnologias e a utilização de métodos avançados de monitoramento podem transformar a maneira como as indústrias operam, garantindo não apenas a eficiência dos sistemas, mas também a segurança e o bem-estar dos trabalhadores.
Erros Comuns no Alinhamento de Redutores
O alinhamento de redutores é uma etapa crucial no funcionamento eficiente de qualquer sistema mecânico. Porém, mesmo com as melhores intenções, muitos operadores e técnicos podem cometer erros que podem comprometer a operação dos equipamentos. Neste artigo, vamos abordar os erros mais comuns que ocorrem durante o alinhamento de redutores, suas consequências e como evitá-los, garantindo assim uma operação mais suave e eficiente.
1. Falta de Preparação e Planejamento
Um dos principais erros no alinhamento de redutores é a falta de preparação adequada antes de iniciar o processo. Ignorar a importância de uma verificação prévia pode levar a medições imprecisas e a ajustes inadequados. Uma preparação cuidadosa envolve:
- Verificar visualmente as condições de montagem dos componentes;
- Asegurar que os suportes e bases estejam limpos e em boas condições;
- Revisar a documentação técnica dos equipamentos, garantindo que todos os parâmetros de operação sejam conhecidos.
Sem essa preparação, o risco de erro aumenta significativamente, resultando em um alinhamento insatisfatório e potencialmente prejudicial ao sistema.
2. Ignorar as Condições Ambientais
As condições ambientais em que os equipamentos operam podem ter um impacto direto no alinhamento de redutores. Fatores como temperatura, umidade e vibrações externas devem ser considerados. Muitas vezes, os técnicos negligenciam esses aspectos, resultando em desalinhamentos durante o funcionamento.
Para evitar este erro, recomenda-se:
- Monitorar a temperatura do ambiente e dos componentes;
- Ter um entendimento claro de como a temperatura afeta os materiais envolvidos;
- Utilizar suportes e bases que minimizem as vibrações externas durante a operação.
3. Medições de Alinhamento Inadequadas
Realizar medições imprecisas é um erro crucial que pode levar a ajustes inadequados. A precisão é essencial no alinhamento de redutores, e qualquer erro nas medições pode resultar em um desalinhamento que comprometerá a operação. Isso pode acontecer por diversos motivos, como:
- Uso de instrumentos de medição descalibrados;
- Falta de habilidades e experiência por parte do operador;
- Desconsideração de erros de paralaxe de medição.
Para garantir medições adequadas, recomenda-se a realização de verificações periódicas dos equipamentos de medição e treinamento dos operadores. O uso de tecnologias avançadas, como alinhadores a laser, pode reduzir significativamente o risco de medições erradas.
4. Desconsiderar Desgastes e Danos nos Componentes
Outro erro comum é desconsiderar o estado físico dos componentes durante o alinhamento. Os redutores e outros elementos associados podem sofrer desgastes ou danos que afetam sua performance e, consequentemente, o alinhamento.
É essencial realizar uma inspeção detalhada para identificar sinais de desgaste, como:
- Falhas visíveis nas engrenagens e rolamentos;
- Desgaste nas superfícies de contato;
- Ruídos ou vibrações incomuns durante a operação.
Se algum dano for identificado, correções devem ser feitas antes de proceder com o alinhamento. Ignorar esses sinais pode comprometer a eficiência operacional e levar a falhas mais sérias, além de aumentar os custos de manutenção.
5. Ajustes Excessivos ou Insuficientes
Quando os operadores realizam ajustes excessivos ou insuficientes, o alinhamento pode sofrer sérias consequências. O excesso de ajustes pode exceder os limites de tolerância, enquanto ajustes insuficientes podem não resolver o problema do desalinhamento.
Para evitar esse erro, é importante seguir procedimentos bem definidos e utilizar instrumentos precisos. Sempre que possível, faça ajustes incrementais e verifique as medições após cada modificação. Isso garantirá que o alinhamento seja feito de forma precisa e segura.
6. Ignorar as Normas e Procedimentos de Segurança
A segurança deve ser uma prioridade em qualquer atividade de manutenção e alinhamento de redutores. Ignorar protocolos de segurança pode levar a acidentes graves. É fundamental garantir que todos os procedimentos de segurança sejam seguidos durante o alinhamento, incluindo:
- Desligar a máquina e assegurar que não há tensão nos componentes;
- Utilizar proteção adequada para os operadores;
- Seguir as diretrizes de manuseio dos equipamentos de medição.
7. Não Documentar o Processo de Alinhamento
A documentação é um componente crucial de qualquer processo de manutenção, incluindo o alinhamento de redutores. Muitas vezes, os técnicos esquecem de registrar as medições e ajustes realizados, o que pode resultar na perda de informações valiosas para diagnósticos futuros.
Para evitar esse erro, recomenda-se:
- Registrar todas as medições feitas antes e depois do alinhamento;
- Documentar qualquer ajuste realizado e suas respectivas razões;
- Criar um histórico de manutenção e alinhamento para cada equipamento.
Esse registro não apenas facilita as futuras manutenções, mas também ajuda a identificar padrões que podem indicar problemas recorrentes.
8. Ignorar a Necessidade de Treinamento Continuado
A manutenção e o alinhamento de redutores são áreas em constante evolução, com novas técnicas e tecnologias emergindo regularmente. No entanto, muitas organizações cometem o erro de não fornecer treinamento contínuo aos seus colaboradores, resultando em obsolescência das habilidades adquiridas e no aumento da probabilidade de erros no alinhamento.
Investir em treinamentos regulares e workshops para a equipe não só aumenta a proficiência, mas também melhora a conscientização sobre a importância do alinhamento e suas implicações no desempenho e na segurança dos equipamentos.
9. Falta de Monitoramento Pós-Alinhamento
Após realizar o alinhamento, é comum que os operadores não realizem um monitoramento adequado para verificar se as correções foram efetivas. Isso pode levar à manutenção de desalinhamentos que poderiam ter sido corrigidos através de revisões simples.
O monitoramento deve incluir:
- Medidas de desempenho do equipamento após o alinhamento;
- Verificações regulares para identificar sinais de desalinhamento;
- Reavaliações constantes das condições de operação e das cargas envolvidas.
10. Conclusão e Melhores Práticas
O alinhamento de redutores é uma tarefa essencial que requer atenção e precisão. Evitar os erros mencionados no artigo pode não apenas aumentar a eficiência operacional, mas também reduzir custos e prolongar a vida útil dos equipamentos. Aqui estão algumas melhores práticas a serem seguidas:
- Realizar uma preparação completa antes do alinhamento;
- Consultar a documentação técnica e prestar atenção às condições ambientais;
- Utilizar instrumentos de medição confiáveis e bem calibrados;
- Inspecionar regularmente os componentes e realizar manutenção conforme necessário;
- Documentar todos os processos de alinhamento e treinar a equipe continuamente.
A adoção de práticas eficazes garantirá não apenas um alinhamento preciso, mas também a operação segura e eficiente dos redutores, reduzindo o risco de falhas e aumentando a produtividade da sua operação.
Manutenção e Melhoria no Alinhamento de Redutores
A manutenção adequada e a melhoria contínua no alinhamento de redutores são essenciais para garantir a eficiência operacional, a segurança e a durabilidade dos equipamentos em qualquer instalação industrial. O alinhamento de redutores não é uma tarefa de uma única vez; é um processo que exige atenção regular e intervenções planejadas para prevenir problemas e maximizar o desempenho. Neste artigo, discutiremos as melhores práticas para a manutenção do alinhamento de redutores, a importância da manutenção preventiva, o papel das tecnologias emergentes e a importância de uma abordagem sistemática para a melhoria contínua.
1. Importância da Manutenção Prevenitiva
A manutenção preventiva é uma estratégia que visa manter os equipamentos em bom estado, evitando falhas e quebras. No caso dos redutores, a manutenção preventiva desempenha um papel crucial no alinhamento. Ela envolve inspeções regulares e ajustes antes que os problemas se tornem críticos. As vantagens da manutenção preventiva incluem:
- Redução de custos: Prevenir falhas é mais econômico do que reparar danos após um incidente. Além disso, evita paradas inesperadas que podem resultar em perda de produção.
- Aumento da vida útil dos equipamentos: A manutenção regular garante que os redutores e outros componentes operem na sua faixa ideal, prolongando sua vida útil.
- Melhoria da segurança: Equipamentos bem mantidos são mais seguros, reduzindo o risco de acidentes e lesões no local de trabalho.
2. Inspeções Regulares e Monitoramento
Um aspecto fundamental da manutenção do alinhamento de redutores é realizar inspeções regulares. Essas inspeções devem incluir:
- Verificação do alinhamento: Use ferramentas de medição apropriadas para verificar se o alinhamento está dentro das tolerâncias especificadas.
- Monitoramento de vibrações: Instalar sistemas de monitoramento de vibrações pode fornecer dados em tempo real sobre o estado do equipamento, ajudando a identificar problemas precocemente.
- Avaliação das condições de operação: Verifique se os redutores estão sendo operados dentro das especificações de temperatura e carga apropriadas.
Essas inspeções devem ser registradas para que você tenha um histórico do desempenho dos redutores e possa identificar tendências que podem indicar um problema emergente.
3. Ajustes Periódicos
O alinhamento não deve ser considerado um evento único; ajustes periódicos são necessários. Isso é crucial em ambientes que podem estar sujeitos a mudanças, como temperaturas variáveis ou vibrações externas. Os ajustes devem ser realizados sempre que:
- Novos componentes forem instalados;
- Houver alterações na configuração do sistema;
- Vibrações excessivas forem detectadas.
Um protocolo bem definido para ajustes deve ser criado e seguido rigorosamente. Isso garantirá que o redutor opere de maneira adequada e minimizará o risco de problemas de alinhamento no futuro.
4. Documentação e Registro
A documentação do processo de manutenção e alinhamento é uma prática vital que muitas vezes é negligenciada. Ter um registro detalhado das inspeções realizadas, medições de alinhamento, ajustes e reparos pode fornecer informações valiosas para futuros diagnósticos e ações corretivas. A documentação deve incluir:
- A data da inspeção e do alinhamento;
- Resultados das medições e observações feitas durante o processo;
- Recomendações para ações futuras e datas programadas para a próxima inspeção.
Essa abordagem sistemática não apenas melhora o entendimento do desempenho do equipamento, mas também prepara a equipe para tomar decisões mais informadas no futuro.
5. Treinamento da Equipe
A capacitação e o treinamento contínuos da equipe são fundamentais para garantir que as práticas de manutenção de redutores sejam seguidas adequadamente. É importante que os operadores e técnicos entendam:
- A importância do alinhamento para a eficiência e segurança;
- As melhores práticas de alinhamento e as técnicas mais apropriadas;
- Como identificar sinais de problemas de alinhamento e agir rapidamente.
Programas de treinamento devem ser atualizados regularmente para incluir as últimas tecnologias e métodos de alinhamento. Além disso, a troca de conhecimento e experiências entre os membros da equipe pode enriquecer o processo de aprendizado e promover um ambiente de trabalho colaborativo.
6. Adoção de Tecnologias Avançadas
Nos últimos anos, o avanço da tecnologia tem revolucionado a forma como os alinhamentos são realizados e monitorados. A adoção de ferramentas e sistemas modernos pode melhorar significativamente a precisão e a eficiência do alinhamento de redutores. Algumas tecnologias úteis incluem:
- Sistemas de Alinhamento a Laser: Esses dispositivos proporcionam resultados de alta precisão e podem economizar tempo durante o processo de alinhamento.
- Monitores de Vibração: Esses sistemas permitem monitorar continuamente o estado do redutor, detectando anomalias que podem indicar problemas de alinhamento.
- Software de Análise de Dados: Programas que coletam dados de desempenho podem ajudar a identificar tendências e prever falhas, permitindo uma manutenção mais proativa.
A integração dessas tecnologias não apenas melhora o alinhamento, mas também contribui para uma cultura de manutenção baseada em dados, onde decisões são tomadas com base em informações precisas.
7. Método de Análise de Causa Raiz
Quando problemas de alinhamento ocorrem repetidamente, a realização de uma análise de causa raiz pode ser extremamente benéfica. Essa abordagem visa identificar a verdadeira causa dos problemas ao invés de apenas tratar os sintomas. A análise pode incluir:
- Revisão dos processos de instalação e alinhamento;
- Análise das condições operacionais e ambientais;
- Entrevistas com a equipe para entender como as tarefas são executadas.
Identificar e corrigir a causa raiz pode prevenir a recorrência de problemas de alinhamento, melhorando a eficiência e reduzindo os custos operacionais a longo prazo.
8. Implementação de Programas de Melhoria Contínua
Adotar uma abordagem sistemática para a melhoria contínua é essencial para manter os redutores alinhados e funcionando de maneira eficiente. Isso envolve:
- Definir metas de desempenho para os redutores;
- Implementar revisões regulares e auditorias de desempenho;
- Incluir feedback da equipe sobre práticas e processos existentes.
Usar metodologias como PDCA (Planejar, Fazer, Verificar, Agir) pode ajudar a estruturar o processo de melhoria contínua e a promover uma cultura de excelência operativa.
9. Colaboração Entre Setores
A colaboração entre diferentes equipes, como manutenção, operações e engenharia, é fundamental para o sucesso das práticas de alinhamento. A comunicação regular permite que as equipes compartilhem informações relevantes, como mudanças nas condições operacionais ou feedback sobre o desempenho do equipamento.
Reuniões regulares de equipe e a criação de uma plataforma para relatórios de problemas e sugestões podem facilitar a colaboração e resultar em melhorias significativas na manutenção e no alinhamento de redutores.
10. Conclusão
A manutenção e melhoria no alinhamento de redutores é um processo contínuo que exige atenção dedicada e uma abordagem sistemática. Implementar práticas eficazes de manutenção preventiva, documentar inspeções e ajustes, adotar tecnologias avançadas e promover o treinamento contínuo da equipe são passos essenciais para garantir que os redutores funcionem de forma eficiente e segura.
Ao investir na manutenção e melhorias do alinhamento, as empresas não apenas prolongam a vida útil de seus equipamentos, mas também melhoram sua eficiência operacional, reduzem custos e criam um ambiente de trabalho mais seguro. O alinhamento de redutores deve ser visto não apenas como uma tarefa técnica, mas como um componente crítico da estratégia de manutenção geral de qualquer instalação industrial.
Em resumo, o alinhamento de redutores é um aspecto vital da manutenção de equipamentos industriais que não deve ser negligenciado. A importância desse alinhamento reflete-se diretamente na eficiência operacional, na segurança dos trabalhadores e na durabilidade dos componentes. Ao aplicar as melhores técnicas de alinhamento e evitar os erros comuns, as empresas podem não apenas otimizar o desempenho de suas máquinas, mas também reduzir custos operacionais e promover um ambiente de trabalho mais seguro. Investir em manutenção preventiva, capacitação da equipe e tecnologias avançadas é essencial para garantir que os redutores funcionem de maneira eficaz e sustentada. Com uma abordagem proativa e estruturada, é possível maximizar a eficiência dos sistemas e assegurar o sucesso das operações industriais.