Alinhamento de eixos de turbinas: tudo que você precisa saber
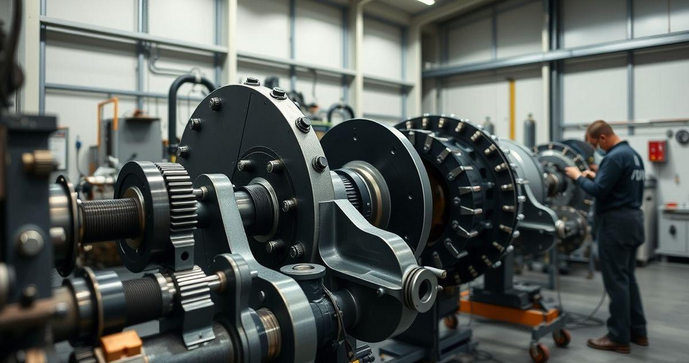
Por: Tiago - 16 de Março de 2025
O que é alinhamento de eixos de turbinas
O alinhamento de eixos de turbinas refere-se ao processo de garantir que os eixos de uma turbina estejam posicionados corretamente em relação uns aos outros e a outros componentes conectados, como motores e redutores. Um alinhamento adequado é crucial para o funcionamento eficiente da turbina, minimizando o desgaste e prevenindo falhas mecânicas.
Existem diversas técnicas utilizadas para realizar esse alinhamento, que podem variar dependendo do tipo de turbina e das especificações do fabricante. O principal objetivo do alinhamento é garantir que os ângulos e distâncias corretas sejam mantidos durante a operação, proporcionando uma rotação suave e evitando vibrações excessivas que podem levar a danos.
Em resumo, o alinhamento de eixos de turbinas é uma prática vital na manutenção industrial, que assegura que o sistema funcione dentro de parâmetros ideais e prolonga a vida útil dos equipamentos envolvidos.
Importância do alinhamento correto
A importância do alinhamento correto de eixos de turbinas não pode ser subestimada. Um alinhamento preciso é fundamental para garantir a eficiência operacional e a longevidade do equipamento.
Quando os eixos estão desalinhados, diversos problemas podem surgir, incluindo aumento de vibrações, desgaste prematuro de componentes e até falhas catastróficas.
Um alinhamento adequado reduz a carga sobre os rolamentos e outros elementos mecânicos, o que se traduz em menos manutenção, menores custos operacionais e um aumento significativo na confiabilidade do sistema.
Além disso, com um alinhamento correto, as turbinas funcionam de maneira mais suave e eficiente, resultando em melhor geração de energia e menor consumo de combustível.
Por consequência, garantir o alinhamento correto de eixos de turbinas é um investimento que traz retornos substanciais em termos de performance, custos e segurança operacional.
Métodos de alinhamento de eixos
Existem diversos métodos para realizar o alinhamento de eixos de turbinas, cada um com suas vantagens e aplicações específicas. Compreender esses métodos pode ajudar na escolha da melhor abordagem para garantir uma operação eficiente e segura.
Método de alinhamento a laser
Um dos métodos mais modernos e precisos é o alinhamento a laser. Este método utiliza feixes de laser para medir a posição dos eixos com alta precisão. Ele é ideal para sistemas que exigem um alinhamento muito rigoroso e pode ser realizado rapidamente, minimizando o tempo de inatividade das máquinas.
Método de alinhamento por fita métrica
Outra abordagem mais tradicional é o alinhamento por fita métrica. Neste método, medidas são tiradas manualmente para determinar o desalinhamento. Embora seja um método mais suscetível a erros humanos, ele pode ser uma solução viável para turbinas em ambientes onde tecnologias mais avançadas não estão disponíveis.
Método de alinhamento com nível de bolha
O uso de um nível de bolha também é uma técnica comum, especialmente em situações onde a precisão extrema não é crítica. Este método envolve verificar a horizontalidade dos eixos e fazer ajustes conforme necessário. É simples, econômico e útil em muitas aplicações.
Método de alinhamento por cordeira
Finalmente, o alinhamento por cordeira consiste em esticar uma corda em torno dos eixos para alinhar visualmente os componentes. Embora menos comum, pode ser útil em situações onde outros equipamentos não estão disponíveis.
Em síntese, cada método de alinhamento tem suas particularidades e deve ser escolhido com base nas especificidades da turbina, nas condições de operação e na precisão desejada.
Sinais de desalinhamento em turbinas
Identificar sinais de desalinhamento em turbinas rapidamente é essencial para evitar danos maiores e custos elevados em manutenção. Aqui estão alguns dos principais sinais que indicam que os eixos podem não estar alinhados corretamente:
1. Vibrações Excessivas
Um dos primeiros sinais de desalinhamento são as vibrações excessivas durante a operação. Essas vibrações são frequentemente percebidas como um ruído incomum e podem ser detectadas tanto auditivamente quanto por meio de dispositivos de monitoramento, podendo causar desgaste acelerado.
2. Aumento da Temperatura
O desalinhamento pode resultar em atrito adicional entre os componentes, o que, por sua vez, leva a um aumento da temperatura dos rolamentos e outros partes móveis da turbina. Monitorar as temperaturas é uma maneira eficaz de identificar problemas de alinhamento.
3. Desgaste Irregular
Desgaste irregular nos rolamentos e eixos é outro sinal claro de problemas de alinhamento. Isso pode se manifestar como ranhuras ou danos visíveis nos componentes, que indicam que estão operando fora dos parâmetros ideais.
4. Ruídos Anormais
Ruídos anormais durante a operação, como batidas ou zumbidos, muitas vezes podem ser atribuídos a uma má condição de alinhamento. Esses sons são geralmente um sinal de que os componentes estão se movendo de maneira inadequada.
5. Flutuações nos Parâmetros de Monitoramento
Muitos sistemas modernos de turbinas estão equipados com sensores que monitoram diversos parâmetros de operação, como pressão, velocidade e temperatura. Flutuações ou leituras inconsistentes em qualquer um destes parâmetros podem indicar problemas de alinhamento.
Reconhecer rapidamente estes sinais pode ajudar a evitar paradas inesperadas e prolongar a vida útil da turbina, além de garantir que o sistema opere com eficiência máxima.
Consequências do desalinhamento
O desalinhamento de eixos em turbinas pode levar a uma série de consequências prejudiciais, não apenas para o próprio equipamento, mas também para a eficiência do sistema como um todo. Aqui estão algumas das principais consequências que podem ocorrer devido ao desalinhamento:
1. Danos Mecânicos
Um dos efeitos mais imediatos do desalinhamento é o aumento do desgaste mecânico nos componentes da turbina, como rolamentos, eixos e engrenagens. Esse desgaste prematuro pode resultar em falhas mecânicas sérias, exigindo reparos dispendiosos ou até mesmo a substituição de componentes.
2. Aumento do Consumo de Energia
Quando um sistema está desalinhado, ele opera de maneira menos eficiente, o que leva a um aumento do consumo de energia. A necessidade de realizar mais trabalho para manter a operação resulta em maiores custos operacionais e, consequentemente, diminuição da rentabilidade.
3. Paradas Não Programadas
Desalinhamentos podem causar falhas inesperadas, levando a paradas não programadas. Essas interrupções podem ser extremamente prejudiciais, resultando em perda de produtividade e custos adicionais de manutenção e reparo.
4. Vibrações Excessivas
As turbinas desalinhadas frequentemente geram vibrações excessivas, o que não apenas afeta o desempenho do equipamento, mas também pode causar danos a estruturas adjacentes e a outros equipamentos conectados.
5. Redução da Vida Útil do Equipamento
Finalmente, o desalinhamento impacta diretamente a vida útil dos componentes. Com maior desgaste e danos frequentes, a longevidade da turbina é significativamente reduzida, resultando em investimentos mais altos para manutenção e substituição.
Portanto, a detecção e correção do desalinhamento em turbinas é crucial para manter a eficiência, segurança e viabilidade econômica do sistema.
Melhores práticas para o alinhamento
Para garantir que o alinhamento de eixos de turbinas seja realizado de maneira eficaz e duradoura, é importante seguir algumas melhores práticas que podem minimizar erros e prolongar a vida útil do equipamento. Aqui estão algumas recomendações essenciais:
1. Realizar Mediçöes Regulares
Realizar medições de alinhamento de forma regular é fundamental para identificar rapidamente quaisquer desalinhamentos. A frequência das medições deve ser determinada com base no uso e nas condições operacionais da turbina.
2. Utilizar Equipamentos de Alinhamento Adequados
Investir em ferramentas de alinhamento de alta qualidade, como sistemas a laser ou alinhadores digitais, pode proporcionar uma maior precisão e facilitar o processo. Ferramentas inadequadas podem levar a medições imprecisas e, consequentemente, a alinhamentos inadequados.
3. Seguir as Instruções do Fabricante
Cada turbina e seus componentes têm especificações específicas. É fundamental seguir as instruções do fabricante para o alinhamento, garantindo que todas as tolerâncias e parâmetros sejam atendidos.
4. Considerar as Condições Ambientais
As condições ambientais, como temperatura e umidade, podem afetar o funcionamento de turbinas e a precisão do alinhamento. Adaptar as práticas de alinhamento para essas condições garante resultados mais confiáveis.
5. Treinar a Equipe de Manutenção
É crucial que a equipe responsável pela manutenção e alinhamento das turbinas esteja bem treinada e atualizada sobre as melhores práticas. Um pessoal bem preparado pode evitar erros e garantir que o trabalho seja feito de forma eficiente e segura.
6. Documentar Todo o Processo
Documentar cada etapa do alinhamento ajuda a manter um histórico das práticas adotadas e das condições dos equipamentos. Isso é útil para identificação de padrões de desgaste e para a implementação de melhorias futuras.
Seguindo essas melhores práticas, você pode garantir que o alinhamento de eixos de turbinas seja realizado com precisão e eficiência, contribuindo para a operação sustentável e econômica do sistema.
Ao longo deste artigo, abordamos a importância do alinhamento de eixos de turbinas, os métodos utilizados para realizá-lo e as consequências do desalinhamento. É evidente que manter um alinhamento adequado é crucial para garantir a eficiência e a longevidade dos equipamentos.
O alinhamento correto não apenas previne danos mecânicos e paradas não programadas, mas também contribui para a redução do consumo de energia e minimiza custos operacionais.
Convidamos você a revisar suas práticas de alinhamento e implementar as melhores práticas discutidas. Isso garantirá que suas turbinas operem de maneira otimizada e sustentável.
E você, está pronto para garantir que o alinhamento de seus eixos esteja sempre em dia? Pense nisso e comece a fazer a diferença hoje mesmo!