Alinhamento de Eixos de Turbinas: Importância e Processo
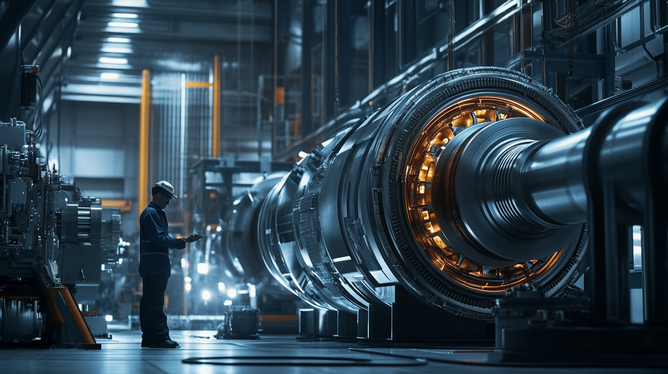
Por: Tiago - 10 de Dezembro de 2024
Alinhamento de eixos de turbinas é um processo crucial que garante a eficiência e a longevidade dos sistemas de turbinas. Quando feito corretamente, evita desgastes excessivos e falhas mecânicas. Neste artigo, iremos explorar a importância do alinhamento, o processo envolvido, as ferramentas necessárias e as consequências do desalinhamento. Continue lendo para entender como garantir a operação ideal de suas turbinas.
Importância do Alinhamento de Eixos de Turbinas
O alinhamento de eixos de turbinas é uma prática fundamental na indústria de energia, principalmente em sistemas que utilizam turbinas a gás ou a vapor. A correta instalação e manutenção deste componente pode fazer toda a diferença na eficiência do equipamento, prolongando sua vida útil e minimizando custos operacionais. Vamos explorar as várias razões pelas quais o alinhamento adequado é tão crucial e o impacto que pode ter em toda a operação.
Eficiência Energética
Uma das principais vantagens do alinhamento de eixos de turbinas é a melhoria na eficiência energética. Eixos desalinhados podem causar perdas significativas na performance do sistema. Quando os eixos não estão alinhados corretamente, as turbinas precisam trabalhar mais para gerar a mesma quantidade de energia. Isso resulta em um aumento do consumo de combustível, que, por sua vez, eleva os custos operacionais e reduz a lucratividade do empreendimento.
Além disso, a eficiência reduzida do sistema pode levar a emissões mais altas, o que é particularmente preocupante em um mundo cada vez mais consciente das questões ambientais. Portanto, manter os eixos alinhados ajuda não apenas na economia, mas também na sustentabilidade ambiental.
Prevenção de Danos Mecânicos
Um dos maiores riscos associados ao desalinhamento de eixos é a possibilidade de danos mecânicos. Desvios menores podem causar vibrações excessivas, levando a um desgaste prematuro de componentes como rolamentos, engrenagens e até mesmo das lâminas das turbinas.
Essas vibrações não só afetarão a integridade física das partes, mas também podem causar interrupções operacionais indesejadas, levando a paradas não planejadas. O tempo de inatividade não só resulta em perda de receita, mas também gera custos adicionais para manutenção e reparo, o que pode ser facilmente evitado com um tratamento adequado do alinhamento de eixos.
Redução de Ruído
Outro aspecto importante a considerar é a redução do nível de ruído gerado pelo sistema. Turbinas desalinhadas tendem a produzir mais barulho devido às vibrações desnecessárias e ao movimento irregular dos componentes internos.
Em ambientes industriais, o controle do ruído é vital, não apenas por questões de conforto, mas também devido a regulamentações de segurança. A manutenção do alinhamento adequado dos eixos pode contribuir significativamente para criar um ambiente de trabalho mais seguro e agradável.
Facilidade de Manutenção
Quando os eixos estão devidamente alinhados, a manutenção preventiva e corretiva torna-se muito mais simples e eficaz. A identificação de problemas potenciais é facilitada, permitindo uma intervenção rápida antes que se tornem problemas significativos que requerem reparos dispendiosos.
Além disso, a troca de peças e componentes requeridos é mais previsível e eficiente, uma vez que menos desgaste e danos ocorrerão em sistemas que operam nas condições ideais. Isso não apenas melhora a confiabilidade do sistema, mas também permite que as equipes de manutenção se concentrem em outras tarefas, aumentando a produtividade geral.
Reliability e Tempo de Atividade
Em um ambiente industrial, a confiabilidade dos sistemas de energia é de extrema importância. Equipamentos que não funcionam corretamente não apenas levam a paradas, mas também afetam toda a cadeia de produção. O alinhamento de eixos de turbinas contribui diretamente para a confiabilidade, garantindo que o sistema funcione de forma contínua e eficiente.
Com o alinhamento adequado, as turbinas podem operar em seus níveis ideais, resultando em maior tempo de atividade e melhor utilização do capital investido. Esta confiabilidade é crucial em aplicações críticas, onde a qualquer falha pode ter consequências graves, tanto financeiras quanto de segurança.
Custos de Operação
Embora existam custos iniciais associados ao alinhamento de eixos de turbinas, os benefícios financeiros a longo prazo superam em muito esses investimentos iniciais. Redução do consumo de energia, menor necessidade de manutenção frequente e prolongamento da vida útil do equipamento resultam em menores custos operacionais e um retorno sobre o investimento mais positivo.
Além disso, ambientes de operação que mantêm seus sistemas em condições otimizadas tendem a ser mais resilientes a choques e quebras, o que novamente se traduz em menos paradas e custos relacionados.
Impacto na Qualidade da Produção
Turbinas desalinhadas não só afetam a eficiência energética e a confiabilidade, mas também podem impactar negativamente na qualidade do produto final em processos industriais. Um sistema que opera fora das especificações pode influir na qualidade do produto, gerando desperdício e necessidade de retrabalho, o que não só aumenta os custos mas também afeta a satisfação do cliente.
Portanto, um alinhamento eficaz dos eixos não apenas melhora a eficiência e reduz custos, mas também assegura a qualidade do produto final, resultando em clientes mais satisfeitos e na possibilidade de repetir negócios.
Implementação de Tecnologias Modernas
Nos últimos anos, a tecnologia avançou significativamente no que diz respeito a alinhamento de eixos, tornando o processo mais preciso e eficiente. Ferramentas como laser e sistemas de monitoramento remoto são cada vez mais comuns, permitindo que empresas realizem o alinhamento de forma muito mais eficaz e com menor intervenção manual.
Essas tecnologias não só aumentam a precisão do alinhamento, mas também possibilitam a coleta de dados em tempo real. Isso permite uma análise cara a cara das condições operacionais e uma tomada de decisão informada, assegurando que o alinhamento e a manutenção sejam realizados com a frequência necessária para evitar problemas futuros.
Conclusão da Importância do Alinhamento
Como vimos, a importância do alinhamento de eixos de turbinas não pode ser subestimada. Desde a eficiência energética até a prevenção de danos mecânicos, as vantagens são numerosas e impactam todos os aspectos operacionais da indústria de energia. Um alinhamento adequado melhora a confiabilidade, reduz custos e melhora a qualidade do produto, além de contribuir para um ambiente de trabalho mais seguro e eficiente.
Portanto, é vital que empresas que operam com turbinas dediquem esforço e recursos para garantir que seus eixos estejam sempre alinhados corretamente. A implementação de tecnologias modernas e práticas recomendadas em manutenção não apenas garantirá a eficiência e a eficácia dos sistemas, mas também resultará em um investimento mais inteligente a longo prazo.
Processo de Alinhamento de Eixos
O processo de alinhamento de eixos de turbinas é uma etapa crucial que deve ser realizada com precisão e atenção aos detalhes. O objetivo principal deste procedimento é garantir que os eixos estejam perfeitamente alinhados para minimizar o desgaste e maximizar a eficiência do sistema. Neste artigo, vamos detalhar o passo a passo do processo de alinhamento, incluindo técnicas, equipamentos e considerações importantes que devem ser levadas em conta.
Preparação para o Alinhamento
Antes de iniciar o processo de alinhamento propriamente dito, é essencial realizar uma preparação adequada. Essa fase envolve a coleta de informações sobre o equipamento, as condições ao redor e o próprio sistema de turbinas.
- Inspeção Visual: Realize uma inspeção visual detalhada nas turbinas e nos eixos. Procure por sinais de desgaste, corrosão, vazamentos ou outros problemas que possam afetar o alinhamento. A identificação de esses problemas antecipadamente pode evitar complicações durante o processo.
- Avaliação do Estado dos Componentes: Verifique as condições dos rolamentos, acoplamentos e outras peças que podem afetar o alinhamento. Substituir partes desgastadas ou danificadas é essencial para garantir um alinhamento bem-sucedido.
- Recolhimento de Dados: Registre as medidas iniciais dos eixos e suas posições relativas antes do alinhamento. Esses dados servirão como base para futuras comparações e ajustes.
Técnicas de Alinhamento
Existem várias técnicas disponíveis para o alinhamento de eixos de turbinas. A escolha da técnica mais adequada dependerá das características específicas do sistema e das ferramentas disponíveis. Aqui estão algumas das técnicas mais comuns:
Alinhamento a LaserO alinhamento a laser é uma das técnicas mais modernas e precisas. Esta técnica utiliza lasers para medir a diferença de alinhamento em tempo real. A precisão é um dos principais benefícios do alinhamento a laser, pois este método minimiza as margens de erro, tornando o alinhamento muito mais eficiente.
- Instalação do Sistema: A configuração do sistema de alinhamento a laser envolve posicionar um dispositivo laser em um eixo, que emite um feixe de luz. Um receptor é colocado no outro eixo para captar o feixe.
- Leitura e Ajuste: O operador observa as leituras do receptor e ajusta os eixos conforme necessário. O alinhamento é considerado ideal quando a luz do laser atinge o receptor em um determinado ponto, indicando que os eixos estão alinhados.
Esta técnica envolve o uso de instrumentos de medição, como níveis e régua. Embora essas ferramentas sejam mais tradicionais, ainda são eficazes, especialmente em ambientes onde a tecnologia a laser não pode ser aplicada.
- Uso de Níveis: Levels são utilizados para avaliar se os eixos estão em um nível horizontal ou vertical. O ponto central de cada eixo é medido para garantir que as alturas são iguais.
- Medição da Distância: A distância entre os eixos é medida em vários pontos e comparada com as especificações do fabricante. Se houver uma diferença, os eixos devem ser ajustados.
Ajustes Durante o Alinhamento
Após determinar a técnica de alinhamento e preparar o local de trabalho, o próximo passo é realizar os ajustes necessários nos eixos. Isso pode envolver o ajuste pela movimentação de suportes ou a adição de calços. Vejamos como isso pode ser feito:
Ajuste de SuportesOs suportes dos eixos podem precisar ser ajustados para corrigir possíveis desalinhamentos. O ajuste destes componentes é crucial para garantir que os eixos fiquem na posição correta. Isso pode envolver o aperto ou afrouxamento de parafusos que fixam os suportes ao corpo principal da turbina.
Uso de CalçosCalços podem ser utilizados para elevar um dos eixos, se necessário. Essa técnica é especialmente útil em ambientes onde há dificuldade em ajustar os suportes. Os calços devem ser escolhidos com cuidado para garantir que não causem instabilidade ou vibração adicional.
Verificação do Alinhamento
Depois que os ajustes forem feitos, é indispensável realizar nova verificação do alinhamento. Isso garante que quaisquer alterações tenham sido eficazes e que os eixos estão agora corretamente alinhados. Veja como isso deve ser feito:
- Repetir Medições: Novas medições devem ser feitas usando a mesma técnica que foi aplicada inicialmente. Isso assegura que o alinhamento esteja em conformidade com as especificações desejadas.
- Ajustes Finais: Se o alinhamento ainda não estiver dentro dos padrões esperados, ajustes adicionais deverão ser feitos até que o resultado desejado seja alcançado.
Documentação e Monitoramento
Uma vez que o alinhamento tenha sido finalizado e as medições confirmadas, é crucial documentar todo o processo. Isso não só é importante para registros futuros, mas também permite o monitoramento do desempenho do sistema. Aqui estão algumas etapas recomendadas:
- Registro dos Resultados: Anote todos os dados relevantes, incluindo medições iniciais, ajustes feitos e medições finais. Isso oferece uma visão geral que pode ser utilizada para futuros trabalhos de manutenção.
- Criação de um Cronograma de Manutenção: Com base nas informações coletadas, é prudente implementar um cronograma de manutenção regular que inclua verificações periódicas do alinhamento. Isso ajudará a evitar problemas futuros e a garantir que o sistema opere sempre em sua capacidade ideal.
- Monitoramento em Tempo Real: Sempre que possível, utilize sistemas de monitoramento em tempo real que forneçam dados contínuos sobre o alinhamento. Isso possibilita intervenções rápidas em caso de desvios ou problemas.
Considerações Finais
O processo de alinhamento de eixos de turbinas é uma operação complexa, mas extremamente importante para o dispositivo e a operação da turbina como um todo. Seguir um procedimento descrito, utilizando técnicas adequadas e ferramentas eficazes, é crucial para garantir a eficiência e a vida útil dos componentes do sistema.
Além disso, a documentação adequada e o monitoramento contínuo são indispensáveis para a manutenção proativa e para evitar problemas futuros. Investir em um bom alinhamento não só assegura um funcionamento ideal das turbinas, mas também pode gerar economias substanciais e contribuir para a sustentabilidade ambiental.
Portanto, nunca subestime a importância do alinhamento de eixos. Um pequeno investimento em cuidados adequados pode traduzir-se em um retorno financeiro e operacional significativo a longo prazo, mantendo as turbinas em operação nas melhores condições possíveis.
Ferramentas Usadas no Alinhamento
O alinhamento de eixos de turbinas é uma atividade técnica que exige precisão e a utilização de ferramentas apropriadas. Escolher as ferramentas corretas é fundamental para garantir que o processo de alinhamento seja bem-sucedido e que os eixos permaneçam adequadamente alinhados ao longo do tempo. Neste artigo, vamos explorar as principais ferramentas usadas no alinhamento de eixos, suas funções e como utilizá-las de maneira efetiva.
Instrumentos de Medição Tradicionais
Os instrumentos de medição tradicionais, embora considerados mais antigos em comparação com a tecnologia moderna, ainda desempenham um papel vital no processo de alinhamento de eixos. A precisão e a confiabilidade desses instrumentos são inegáveis, proporcionando resultados satisfatórios quando utilizados corretamente.
Nível de BolhaO nível de bolha é um instrumento simples que ajuda a verificar a horizontalidade ou verticalidade de uma superfície. No contexto do alinhamento de eixos, o nível de bolha pode ser utilizado para assegurar que os eixos estão alinhados horizontalmente.
- Uso: Coloque o nível de bolha sobre o eixo e observe a bolha no tubo de vidro. Se a bolha estiver centrada entre as marcações, o eixo está nivelado. Se não estiver, ajustes devem ser feitos.
- Vantagem: O nível de bolha é acessível e fácil de usar, tornando-se uma ferramenta útil para verificações rápidas no alinhamento.
A trena ou fita métrica é essencial para medições precisas de distâncias entre os pontos de referência nos eixos. Ela ajuda a identificar o quanto os eixos estão desalinhados e é indispensável durante as verificações iniciais e os ajustes.
- Uso: Meça a distância entre os centros dos eixos em diferentes pontos e compare as medições com as especificações do fabricante.
- Vantagem: A simplicidade da trena ou fita métrica permite que qualquer operador realize medições de forma rápida e eficiente.
Instrumentos de Alinhamento a Laser
Nos últimos anos, o uso de laser para alinhamento de eixos tornou-se cada vez mais popular devido à sua precisão e eficiência. As ferramentas a laser ajudam a visualizar melhor os eixos e a reduzir os erros humanos, resultando em alinhamentos mais eficazes e rápidos.
Equipamento de Alinhamento a LaserO equipamento de alinhamento a laser consiste em dois dispositivos principais: um transmissor de laser e um receptor. O transmissor projeta um feixe de laser e o receptor capta esse feixe. Essa tecnologia permite medições em tempo real, o que torna o ajuste mais dinâmico.
- Uso: Posicione o transmissor em um dos eixos e o receptor no eixo oposto. O sistema calcula automaticamente as diferenças de alinhamento e fornece feedback instantâneo.
- Vantagem: A precisão é significativamente aumentada, uma vez que as medições são feitas em tempo real com pequenas margens de erro.
Calibradores e Condutores de Alinhamento
Calibradores e condutores são ferramentas utilizadas para ajustar o alinhamento baseando-se nas medições obtidas. Estes dispositivos ajudam a garantir que os eixos sejam ajustados corretamente após as medições, mantendo a exatidão.
Calibrador de DistânciaUm calibrador de distância é uma ferramenta que mede a distância entre os eixos, garantindo que os ajustes feitos sejam precisos.
- Uso: Após o alinhamento inicial, o calibrador pode ser utilizado para verificar se os eixos estão na distância correta.
- Vantagem: Aumenta a confiança de que os eixos estão não apenas alinhados, mas também na distância correta entre si.
Os condutores de alinhamento são usados para garantir que ambos os eixos estejam em linha uns com os outros e que os ângulos estejam corretos.
- Uso: Os condutores são colocados em ambas as extremidades dos eixos e ajudam a verificar a linha de alinhamento durante o ajuste.
- Vantagem: Permitem um uso fácil e eficaz para garantir a correção do alinhamento anguloso.
Ferramentas de Ajuste
Além das ferramentas de medição, é necessário dispor de ferramentas para fazer os ajustes necessários após as medições. As ferramentas de ajuste são essenciais para garantir que a posição dos eixos seja corrigida de forma adequada, garantindo resultados eficazes.
Chaves de Fenda e Chaves InglesasEssas ferramentas são usadas para apertar ou afrouxar os parafusos que fixam os eixos nos suportes. A qualidade do alinhamento pode depender da capacidade de ajustar estes parafusos com precisão.
- Uso: Utilize chaves de fenda e chaves inglesas para fazer os ajustes nos suportes dos eixos após as medições.
- Vantagem: Ferramentas manuais disponíveis que podem ser utilizadas em várias aplicações, ideal para pequenos ajustes.
Os calços são usados para elevar um eixo em relação ao outro, quando necessário, para corrigir o desalinhamento. Eles devem ser utilizados com cuidado, de modo a não criar instabilidade.
- Uso: Insira calços sob o suporte do eixo que necessita de elevação e verifique as medições novamente.
- Vantagem: Proporciona uma solução rápida e eficaz para corrigir pequenas diferenças de altura.
Softwares de Alinhamento
Com o avanço da tecnologia digital, muitos profissionais estão adotando softwares específicos para auxiliar no processo de alinhamento. Esses softwares podem trabalhar em conjunto com equipamentos de medição e alinhamento, permitindo análises detalhadas e relatórios precisos sobre o estado do alinhamento dos eixos.
- Uso: Os softwares podem coletar dados de equipamentos de medição a laser ou outros dispositivos, proporcionando uma análise precisa do alinhamento e gerando relatórios que destacam áreas que precisam de ajuste.
- Vantagem: O uso de software não só aumenta a precisão como também simplifica o processo, permitindo que as equipes prevejam manutenções futuras com base nos dados analisados.
Considerações Finais
As ferramentas utilizadas no alinhamento de eixos de turbinas são vitais para a operação bem-sucedida e eficiente deste tipo de sistema. Desde instrumentos de medição tradicionais como níveis e trenas até tecnologias modernas como alinhamento a laser e softwares especializados, cada ferramenta desempenha um papel crítico no processo de alinhamento.
Investir em boas ferramentas não só economiza dinheiro ao evitar manutenção frequente e dispendiosa, mas também garante que o sistema opere de maneira eficaz, reduzindo o consumo de energia e prevenindo falhas mecânicas. Cada técnica e ferramenta deve ser escolhida e utilizada com base na experiência e nas necessidades específicas do local de operação.
Portanto, na hora de realizar o alinhamento de eixos de turbinas, lembre-se da importância de utilizar as ferramentas corretas e seguir as práticas recomendadas para garantir que seu equipamento funcione sob as melhores condições possíveis. Combinando boa prática com as ferramentas certas, é possível maximizar a eficiência, aumentar a vida útil dos componentes e garantir um ambiente de trabalho seguro e produtivo.
Consequências do Desalinhamento de Eixos
O desalinhamento de eixos em turbinas e outros sistemas rotativos não é um problema que deve ser subestimado. A falta de alinhamento apropriado pode gerar uma série de consequências negativas que afetam não apenas o desempenho do equipamento, mas também a segurança e a eficiência econômica de toda a operação. Neste artigo, vamos explorar as principais consequencias do desalinhamento de eixos, dando uma visão detalhada sobre os riscos, custos envolvidos e a importância de manter o alinhamento adequado.
Desgaste Prematuro de Componentes
Uma das consequências mais críticas do desalinhamento de eixos é o desgaste prematuro dos componentes do sistema. Quando os eixos não estão alinhados, a força gerada pelo movimento rotativo não é distribuída uniformemente, o que pode levar a um aumento desproporcional de tensão em várias partes do equipamento.
- Rolamentos: Os rolamentos são particularmente afetados por forças irregulares. Quando atolados em condições de desalinhamento, eles podem sofrer com desgaste acelerado, aumentando a necessidade de manutenção e substituição.
- Engrenagens: O desalinhamento pode ter um impacto significativo em como as engrenagens se encaram uma na outra, gerando um estresse excessivo que pode levar a falhas. Isso pode resultar em custos altos de reparação e substituição.
Aumento de Vibrações
Um sistema desalinhado tem maior propensão a vibrações indesejadas. Essas vibrações podem causar uma série de problemas, incluindo ruídos excessivos, desconforto para os operadores e a degradação de componentes mecânicos.
- Vibrações Nocivas: As vibrações provocadas pelo desalinhamento podem ser perigosas, contribuindo para a fadiga do material e possivelmente levando a quebras catastróficas do equipamento.
- Monitoramento Complicado: A detecção de problemas pode se tornar mais difícil em um sistema que opera sob vibrações inconsistentes, resultando em diagnósticos inadequados de problemas.
Perda de Eficiência Energética
O desalinhamento dos eixos não apenas afeta a durabilidade do equipamento, mas também a eficiência operacional. Quando os eixos não estão em alinhamento, as turbinas precisam trabalhar mais para gerar a mesma quantidade de energia. Este aumento no esforço resulta em um consumo excessivo de energia.
- Aumento de Custos de Energia: O consumo energético elevado se traduz diretamente em custos operacionais mais altos. As empresas podem acabar gastando muito mais do que o necessário apenas para manter suas operações.
- Redução na Capacidade de Geração: Em sistemas de turbinas, uma redução de eficiência pode resultar em menor output de energia, comprometendo a demanda e a lucratividade.
Paradas Não Planejadas
Outra grande consequência do desalinhamento é a ocorrência de paradas não planejadas. Sistemas que não operam corretamente têm um risco maior de falhas súbitas, o que pode resultar em paradas indesejadas que afetam a produção e aumentam os custos de manutenção.
- Interrupções na Produção: Dependendo do tipo de operação, uma parada inesperada pode interromper a produção por longos períodos, retardando a entrega de produtos e levando à insatisfação do cliente.
- Custos de Reparos: Reparar um equipamento que quebrou devido ao desalinhamento pode ser excessivamente caro, especialmente quando as peças precisam ser substituídas.
Diminuição da Qualidade do Produto
O desalinhamento de eixos pode afetar não apenas a eficiência e a operação do sistema, mas também a qualidade do produto final. Em sistemas industriais, a qualidade é muitas vezes diretamente impactada pela precisão do alinhamento dos eixos.
- Produção de Rejeitos: O desalinhamento pode levar a produtos finais que não atendem às especificações desejadas, resultando em um aumento de rejeições e retrabalho.
- Satisfação do Cliente: A inconsistência na qualidade do produto pode levar à insatisfação do cliente, impactando a reputação da empresa e suas relações comerciais.
Riscos para a Segurança
O desalinhamento não é um problema apenas mecânico; também deve ser considerado em um contexto de segurança. Sistemas que operam fora das especificações podem causar acidentes e ferimentos a funcionários e operadores.
- Quedas e Acidentes: Máquinas que falham devido a desalinhamento podem causar acidentes graves, provocando danos físicos aos operadores e gerando riscos legais para a empresa.
- Custo com Segurança: Aumento de despesas com seguros, treinamento e procedimentos de segurança decorrentes de problemas gerados por desalinhamento.
Interferência na Manutenção Rotineira
Manter um programa de manutenção eficiente é vital para a longevidade e o desempenho do equipamento. No entanto, o desalinhamento pode dificultar essa tarefa e tornar a manutenção mais complexa e demorada.
- Complicações de Diagnóstico: A vibração excessiva e o desgaste irregular podem dificultar a identificação de quais componentes precisam de atenção, atrasando o processo de manutenção.
- Aumento das Diligências de Manutenção: As empresas podem ser forçadas a realizar manutenções mais frequentes, aumentando a carga de trabalho e os custos de operação ao longo do tempo.
Aumento dos Custos Operacionais
Todos os problemas mencionados resultam em um impacto significativo nos custos operacionais. O desalinhamento não só afeta individualmente várias peças do equipamento, mas também gera custos indiretos que podem acumular rapidamente.
- Synergistic Costs: A soma dos custos operacionais elevados, custos com reparos, manutenção frequente e perda de produção pode sobrecarregar drasticamente as finanças de uma empresa.
- Retorno sobre Investimento: A falta de alinhamento pode reduzir a eficiência geral e, consequentemente, o retorno sobre o investimento torna-se mais difícil de alcançar.
Problemas de Reputação e Credibilidade
A longo prazo, as consequências do desalinhamento de eixos não se limitam apenas a perdas financeiras e operacionais, mas também podem impactar negativamente a reputação da empresa.
- Divulgação de Problemas: Casos frequentes de falhas e paradas inesperadas podem vir a público, afetando a percepção da marca e a confiança dos clientes e investidores.
- Impacto na Relação com Fornecedores: Problemas contínuos de produção podem interferir nas relações comerciais e na negociação com fornecedores, que podem ver a empresa como menos confiável.
Considerações Finais
As consequências do desalinhamento de eixos em turbinas e outros sistemas rotativos são extensas e multifacetadas. Desde o desgaste prematuro de componentes, passando por vibrações indesejadas e perda de eficiência, até questões de segurança e impacto em reputação, todos estes fatores ressaltam a importância de manter os eixos devidamente alinhados.
Para empresas que buscam minimizar custos e maximizar eficiência, a implementação de práticas regulares de alinhamento e manutenção não é opcional, mas uma necessidade. Investir em boas ferramentas de alinhamento, em tecnologia adequada e em capacitação de pessoal pode não apenas evitar os problemas enumerados, mas também proporcionar um ambiente operacional mais seguro e eficiente.
Portanto, é crucial que todos os envolvidos na operação e na manutenção de turbinas e sistemas rotativos entendam as graves consequências que o desalinhamento pode provocar. A proatividade na manutenção e o foco no controle de qualidade são fundamentais para garantir operações bem-sucedidas e minimizar riscos a longo prazo.
Concluindo, o alinhamento de eixos de turbinas é uma prática indispensável para assegurar o desempenho ótimos desses sistemas. Os riscos associados ao desalinhamento, como desgaste excessivo, aumento do consumo de energia e paradas não planejadas, sublinham a importância de uma abordagem proativa na manutenção. Compreender as ferramentas e técnicas necessárias para o alinhamento é fundamental para proteger o investimento em equipamentos e garantir a eficiência operacional. Ao priorizar o alinhamento e adotar práticas regulares de manutenção, as empresas não apenas evitam problemas dispendiosos, mas também melhoram sua produtividade e a qualidade do produto final. Portanto, cuidar do alinhamento dos eixos é um passo essencial para um funcionamento seguro e eficaz das turbinas, levando a resultados positivos a longo prazo.