Alinhamento a Laser de Eixos é Essencial para a Manutenção Eficiente de Máquinas
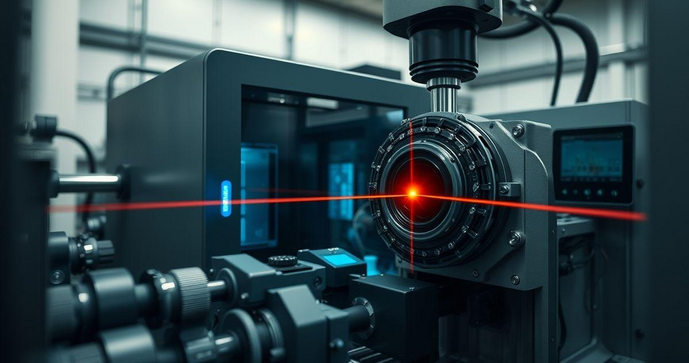
Por: Tiago - 19 de Março de 2025
O alinhamento a laser de eixos é uma técnica fundamental para garantir o desempenho ideal de máquinas e equipamentos industriais. Com a precisão que essa tecnologia oferece, é possível minimizar o desgaste de componentes, aumentar a eficiência operacional e reduzir custos com manutenção. Neste artigo, abordaremos as vantagens do alinhamento a laser, como o processo é realizado, os erros comuns a serem evitados e os cuidados necessários após a execução do alinhamento.
Vantagens do Alinhamento a Laser de Eixos na Indústria
O alinhamento a laser de eixos é uma técnica moderna que revolucionou a forma como as indústrias realizam a manutenção de suas máquinas. Com a precisão e a eficiência que essa tecnologia proporciona, as empresas têm conseguido otimizar seus processos e reduzir custos operacionais. A seguir, exploraremos as principais vantagens do alinhamento a laser de eixos na indústria.
Uma das principais vantagens do alinhamento a laser é a precisão. Ao contrário dos métodos tradicionais, que podem ser suscetíveis a erros humanos e variáveis ambientais, o alinhamento a laser utiliza feixes de luz para determinar a posição exata dos eixos. Isso resulta em um alinhamento muito mais preciso, com desvios que podem ser medidos em milésimos de milímetro. Essa precisão é crucial para garantir que as máquinas operem de forma eficiente e sem desgastes excessivos.
Além da precisão, o alinhamento a laser também oferece uma significativa redução no tempo de manutenção. Os métodos tradicionais de alinhamento podem ser demorados, exigindo várias medições e ajustes. Com o alinhamento a laser, o processo é simplificado e acelerado, permitindo que os técnicos realizem o alinhamento em uma fração do tempo. Isso não apenas aumenta a eficiência da manutenção, mas também minimiza o tempo de inatividade das máquinas, o que é vital para a produtividade industrial.
Outra vantagem importante é a redução do desgaste dos componentes. Quando os eixos não estão alinhados corretamente, isso pode causar um desgaste irregular em rolamentos, engrenagens e outros componentes mecânicos. O alinhamento a laser ajuda a garantir que as forças sejam distribuídas uniformemente, prolongando a vida útil dos componentes e reduzindo a necessidade de substituições frequentes. Isso se traduz em economias significativas em custos de manutenção e reposição de peças.
O alinhamento a laser também contribui para a melhoria da eficiência energética. Máquinas que operam com eixos desalinhados tendem a consumir mais energia, uma vez que precisam trabalhar mais para superar a resistência adicional causada pelo desalinhamento. Com o alinhamento adequado, as máquinas funcionam de maneira mais eficiente, resultando em uma redução no consumo de energia. Isso não apenas diminui os custos operacionais, mas também contribui para práticas mais sustentáveis dentro da indústria.
Além disso, o alinhamento a laser proporciona um ambiente de trabalho mais seguro. Máquinas desalinhadas podem gerar vibrações excessivas, que não apenas afetam o desempenho, mas também podem representar riscos à segurança dos operadores. Com o alinhamento correto, as vibrações são minimizadas, reduzindo o risco de falhas mecânicas e acidentes de trabalho. Isso é especialmente importante em ambientes industriais, onde a segurança dos funcionários deve ser uma prioridade.
Outro aspecto a ser considerado é a facilidade de uso dos equipamentos de alinhamento a laser. A maioria dos sistemas modernos é projetada para ser intuitiva e fácil de operar, permitindo que até mesmo técnicos com menos experiência possam realizar o alinhamento de forma eficaz. Isso reduz a necessidade de treinamento extensivo e permite que as empresas aproveitem ao máximo essa tecnologia sem complicações.
O alinhamento a laser também oferece a vantagem de fornecer relatórios detalhados sobre o processo de alinhamento. Esses relatórios podem incluir dados sobre a condição dos eixos antes e depois do alinhamento, bem como informações sobre a necessidade de manutenção futura. Essa documentação é valiosa para as equipes de manutenção, pois permite um acompanhamento mais eficaz das condições das máquinas e ajuda na tomada de decisões informadas sobre futuras intervenções.
Por fim, o alinhamento a laser de eixos pode ser integrado a programas de manutenção preditiva. Ao monitorar continuamente o alinhamento e as condições das máquinas, as empresas podem identificar problemas antes que se tornem críticos, permitindo intervenções proativas e evitando paradas inesperadas. Isso não apenas melhora a confiabilidade das operações, mas também contribui para uma gestão mais eficiente dos recursos.
Em resumo, as vantagens do alinhamento a laser de eixos na indústria são numerosas e impactantes. Desde a precisão e a redução do tempo de manutenção até a diminuição do desgaste dos componentes e a melhoria da eficiência energética, essa tecnologia se mostra essencial para a manutenção moderna. Para empresas que buscam otimizar suas operações e garantir a longevidade de seus equipamentos, o alinhamento a laser é uma solução que não pode ser ignorada. Para mais informações sobre como manter seus equipamentos em ótimo estado, confira a Manutenção de redutores .
Como Funciona o Processo de Alinhamento a Laser
O processo de alinhamento a laser é uma técnica avançada que utiliza a tecnologia de feixes de luz para garantir que os eixos de máquinas e equipamentos estejam perfeitamente alinhados. Essa abordagem não apenas melhora a eficiência operacional, mas também prolonga a vida útil dos componentes mecânicos. Neste artigo, vamos explorar como funciona o processo de alinhamento a laser, desde a preparação até a execução e verificação dos resultados.
O primeiro passo no processo de alinhamento a laser é a preparação do equipamento e do ambiente de trabalho. Antes de iniciar, é fundamental garantir que a máquina esteja desligada e que todas as partes móveis estejam paradas. Isso é crucial para a segurança dos operadores e para a precisão do alinhamento. Além disso, é importante limpar a área ao redor dos eixos, removendo qualquer sujeira ou obstrução que possa interferir na medição.
Uma vez que a área está limpa e segura, o próximo passo é instalar os dispositivos de alinhamento a laser. Esses dispositivos geralmente consistem em um transmissor e um receptor. O transmissor emite um feixe de laser que é direcionado ao receptor, que pode ser posicionado em diferentes pontos ao longo do eixo. A instalação deve ser feita de forma cuidadosa, garantindo que o transmissor esteja fixo e estável, pois qualquer movimento pode comprometer a precisão das medições.
Após a instalação dos dispositivos, o técnico deve calibrar o sistema. A calibração é um passo crítico que garante que o equipamento esteja funcionando corretamente e que as medições sejam precisas. Isso envolve ajustar o alinhamento do laser e verificar se o feixe está nivelado. A maioria dos sistemas modernos de alinhamento a laser possui recursos de auto calibração, o que facilita esse processo e minimiza a margem de erro.
Com o sistema calibrado, o técnico pode iniciar o processo de medição. O transmissor emite o feixe de laser, que é captado pelo receptor. O sistema registra a posição do feixe em relação aos eixos da máquina. Essa medição é feita em diferentes pontos, permitindo que o técnico identifique qualquer desalinhamento. O software associado ao sistema de alinhamento a laser processa essas informações e gera um relatório detalhado, mostrando a condição atual dos eixos e as correções necessárias.
Uma das grandes vantagens do alinhamento a laser é a capacidade de realizar medições em tempo real. Isso significa que o técnico pode observar imediatamente os resultados e fazer ajustes conforme necessário. Se o sistema indicar que os eixos estão desalinhados, o técnico pode proceder com as correções. Isso geralmente envolve o ajuste das bases ou suportes dos eixos, utilizando ferramentas específicas para garantir que as alterações sejam feitas com precisão.
Após realizar os ajustes, o técnico deve repetir o processo de medição para verificar se o alinhamento foi corrigido. Essa etapa é fundamental, pois garante que as alterações feitas realmente resolveram o problema de desalinhamento. O sistema de alinhamento a laser permite que o técnico visualize as melhorias em tempo real, facilitando a identificação de qualquer necessidade de ajuste adicional.
Uma vez que o alinhamento esteja correto, o técnico pode finalizar o processo. Isso inclui a documentação dos resultados, que é uma parte importante do processo de manutenção. O relatório gerado pelo sistema de alinhamento a laser pode ser utilizado para futuras referências e para monitorar a condição dos eixos ao longo do tempo. Essa documentação é valiosa para a gestão de manutenção, pois permite que as empresas acompanhem o desempenho de suas máquinas e identifiquem padrões de desgaste.
Além disso, o alinhamento a laser pode ser integrado a programas de manutenção preditiva. Isso significa que, ao monitorar continuamente o alinhamento dos eixos, as empresas podem identificar problemas antes que se tornem críticos. Essa abordagem proativa ajuda a evitar paradas inesperadas e a garantir que as máquinas operem de forma eficiente.
Em resumo, o processo de alinhamento a laser envolve uma série de etapas que vão desde a preparação do ambiente até a medição e verificação dos resultados. A precisão e a eficiência dessa técnica a tornam uma escolha ideal para a manutenção de máquinas industriais. Para mais informações sobre como implementar essa tecnologia em sua empresa, confira o Alinhamento a laser e descubra como ele pode beneficiar suas operações.
Erros Comuns no Alinhamento de Eixos e Como Evitá-los
O alinhamento de eixos é uma etapa crucial na manutenção de máquinas industriais, pois um alinhamento inadequado pode levar a falhas mecânicas, aumento do desgaste e custos elevados com reparos. Apesar da importância desse processo, muitos técnicos ainda cometem erros que podem comprometer a eficiência das máquinas. Neste artigo, abordaremos os erros mais comuns no alinhamento de eixos e como evitá-los, garantindo um desempenho ideal dos equipamentos.
Um dos erros mais frequentes é a falta de preparação adequada antes de iniciar o alinhamento. Muitas vezes, os técnicos começam o processo sem garantir que a máquina esteja em condições ideais. Isso inclui não verificar se a máquina está desligada, se todas as partes móveis estão paradas e se a área ao redor está limpa. A falta de preparação pode resultar em medições imprecisas e, consequentemente, em um alinhamento inadequado. Para evitar esse erro, é fundamental seguir um checklist de preparação que inclua todas as etapas necessárias antes de iniciar o alinhamento.
Outro erro comum é a calibração inadequada do equipamento de alinhamento. A calibração é um passo crítico que garante que o sistema esteja funcionando corretamente. Se o equipamento não estiver calibrado, as medições podem ser imprecisas, levando a um desalinhamento. Para evitar esse problema, os técnicos devem sempre seguir as instruções do fabricante para a calibração do equipamento e realizar verificações regulares para garantir que o sistema esteja em boas condições de funcionamento.
A escolha incorreta do método de alinhamento também pode ser um fator que contribui para erros. Existem diferentes métodos de alinhamento, como o alinhamento a laser e o alinhamento por fita métrica. Cada método tem suas vantagens e desvantagens, e a escolha do método deve ser baseada nas necessidades específicas da máquina e nas condições do ambiente. Para evitar esse erro, é importante que os técnicos estejam bem informados sobre os diferentes métodos de alinhamento e suas aplicações, garantindo que escolham a abordagem mais adequada para cada situação.
Além disso, a falta de atenção aos detalhes durante o processo de medição pode levar a erros significativos. Muitas vezes, os técnicos podem se distrair ou apressar o processo, resultando em medições imprecisas. Isso pode incluir não posicionar corretamente o transmissor e o receptor, não registrar todas as medições necessárias ou não verificar se o feixe de laser está alinhado corretamente. Para evitar esse tipo de erro, é essencial que os técnicos mantenham o foco durante todo o processo e sigam rigorosamente as etapas de medição.
Outro erro que pode ocorrer é a não realização de medições em diferentes pontos. Algumas máquinas podem ter variações em seu alinhamento ao longo de diferentes seções do eixo. Se o técnico realizar medições apenas em um ponto, pode não identificar problemas que existem em outras áreas. Para evitar esse erro, é importante que o técnico faça medições em vários pontos ao longo do eixo, garantindo uma avaliação completa do alinhamento.
A falta de documentação adequada também é um erro comum que pode ter consequências negativas. Muitas vezes, os técnicos não registram os resultados do alinhamento ou não documentam as condições das máquinas antes e depois do processo. Essa falta de documentação pode dificultar a identificação de padrões de desgaste e a tomada de decisões informadas sobre futuras manutenções. Para evitar esse problema, é fundamental que os técnicos mantenham registros detalhados de todos os alinhamentos realizados, incluindo medições, ajustes feitos e quaisquer observações relevantes.
Além disso, a negligência na manutenção dos equipamentos de alinhamento pode levar a erros. Equipamentos desgastados ou danificados podem comprometer a precisão das medições. É importante que as empresas realizem manutenções regulares em seus equipamentos de alinhamento, garantindo que estejam sempre em boas condições de funcionamento. Para mais informações sobre como manter seus equipamentos em ótimo estado, consulte a Manutenção de redutores industriais e descubra como garantir a longevidade de suas máquinas.
Por fim, a falta de treinamento adequado para os técnicos pode ser um fator que contribui para erros no alinhamento de eixos. Técnicos que não estão familiarizados com os equipamentos ou com os métodos de alinhamento podem cometer erros que poderiam ser evitados com um treinamento adequado. Para evitar esse problema, as empresas devem investir em programas de treinamento para seus técnicos, garantindo que eles estejam atualizados sobre as melhores práticas e as tecnologias mais recentes.
Em resumo, os erros comuns no alinhamento de eixos podem ter consequências significativas para a eficiência e a durabilidade das máquinas. Ao evitar erros como a falta de preparação, calibração inadequada, escolha incorreta do método, falta de atenção aos detalhes, medições limitadas, falta de documentação, negligência na manutenção dos equipamentos e falta de treinamento, as empresas podem garantir que seus processos de alinhamento sejam eficazes e que suas máquinas operem de forma ideal. A implementação de boas práticas e a conscientização sobre esses erros são essenciais para o sucesso na manutenção industrial.
Manutenção e Cuidados Após o Alinhamento a Laser de Eixos
Após a realização do alinhamento a laser de eixos, é fundamental implementar uma série de práticas de manutenção e cuidados para garantir que os resultados obtidos sejam mantidos ao longo do tempo. O alinhamento adequado é apenas o primeiro passo para assegurar o desempenho ideal das máquinas; a manutenção contínua é essencial para evitar problemas futuros e prolongar a vida útil dos equipamentos. Neste artigo, discutiremos as principais práticas de manutenção e cuidados que devem ser adotados após o alinhamento a laser de eixos.
Um dos primeiros cuidados a serem tomados após o alinhamento é a verificação das condições de operação da máquina. É importante monitorar o desempenho da máquina nas primeiras horas e dias após o alinhamento. Isso inclui observar se há vibrações anormais, ruídos ou qualquer comportamento que possa indicar um desalinhamento. Caso sejam notados problemas, é recomendável realizar uma nova verificação do alinhamento para identificar e corrigir possíveis falhas.
Além disso, a lubrificação adequada dos componentes é um aspecto crucial da manutenção pós-alinhamento. A lubrificação reduz o atrito entre as partes móveis, minimizando o desgaste e prolongando a vida útil dos componentes. É importante seguir as recomendações do fabricante quanto ao tipo e à frequência de lubrificação. A falta de lubrificação pode levar a um aumento do calor e do desgaste, o que pode resultar em desalinhamento e falhas mecânicas.
Outro cuidado importante é a inspeção regular dos suportes e bases dos eixos. Após o alinhamento, é possível que os suportes precisem de ajustes para garantir que permaneçam firmes e estáveis. Com o tempo, vibrações e forças de operação podem causar afrouxamento dos parafusos e suportes, levando a um desalinhamento gradual. Portanto, é recomendável realizar inspeções periódicas para verificar se os suportes estão devidamente fixados e se não há sinais de desgaste ou danos.
A limpeza dos componentes também deve ser uma parte integrante da manutenção pós-alinhamento. Poeira, sujeira e detritos podem se acumular nas partes móveis e nos eixos, interferindo no funcionamento adequado da máquina. A limpeza regular ajuda a evitar que esses contaminantes causem problemas de alinhamento e desgaste. Utilize produtos de limpeza adequados e evite o uso de solventes que possam danificar os componentes.
Além disso, é importante documentar todos os procedimentos de manutenção realizados após o alinhamento. Manter registros detalhados das inspeções, lubrificações e quaisquer ajustes feitos é essencial para o gerenciamento eficaz da manutenção. Essa documentação pode ser útil para identificar padrões de desgaste e para planejar futuras manutenções. A análise dos registros pode ajudar a prever quando um novo alinhamento pode ser necessário, evitando paradas inesperadas e custos adicionais.
Outro aspecto a ser considerado é a realização de medições periódicas do alinhamento. Mesmo após um alinhamento a laser bem-sucedido, é recomendável realizar medições regulares para garantir que os eixos permaneçam alinhados. Isso é especialmente importante em ambientes industriais onde as máquinas estão sujeitas a vibrações e forças que podem causar desalinhamento ao longo do tempo. A frequência das medições pode variar dependendo do tipo de máquina e das condições de operação, mas uma abordagem proativa pode evitar problemas maiores no futuro.
Além disso, a formação e o treinamento contínuo da equipe de manutenção são fundamentais. Os técnicos devem estar atualizados sobre as melhores práticas de manutenção e alinhamento, bem como sobre as tecnologias mais recentes. Investir em treinamento pode ajudar a garantir que a equipe esteja preparada para lidar com quaisquer problemas que possam surgir e para realizar manutenções de forma eficaz.
Por fim, a integração do alinhamento a laser com um programa de manutenção preditiva pode ser uma estratégia eficaz para garantir a longevidade dos equipamentos. A manutenção preditiva envolve o monitoramento contínuo das condições das máquinas e a realização de intervenções antes que problemas se tornem críticos. Isso pode incluir o uso de sensores e sistemas de monitoramento que alertam a equipe de manutenção sobre quaisquer alterações nas condições de operação, permitindo que ações corretivas sejam tomadas rapidamente.
Em resumo, a manutenção e os cuidados após o alinhamento a laser de eixos são essenciais para garantir que os resultados obtidos sejam mantidos ao longo do tempo. A verificação das condições de operação, a lubrificação adequada, a inspeção regular dos suportes, a limpeza dos componentes, a documentação das manutenções, as medições periódicas, o treinamento da equipe e a integração com programas de manutenção preditiva são práticas que contribuem para a eficiência e a durabilidade das máquinas. Para mais informações sobre como manter seus equipamentos em ótimo estado, consulte a Manutenção de redutores de velocidade e descubra como garantir a longevidade de suas máquinas.
Em conclusão, o alinhamento a laser de eixos se destaca como uma solução essencial para a manutenção industrial, proporcionando benefícios significativos em termos de precisão, eficiência e durabilidade dos equipamentos. Ao compreender as vantagens dessa técnica, o processo de alinhamento, os erros a serem evitados e a importância da manutenção contínua, as empresas podem otimizar suas operações e reduzir custos a longo prazo. Investir em alinhamento a laser não apenas melhora o desempenho das máquinas, mas também contribui para um ambiente de trabalho mais seguro e produtivo. Portanto, adotar essa tecnologia é um passo crucial para qualquer organização que busca excelência em suas operações industriais.