Alinhamento a Laser de Eixos: A Solução Eficiente para Máquinas Industriais
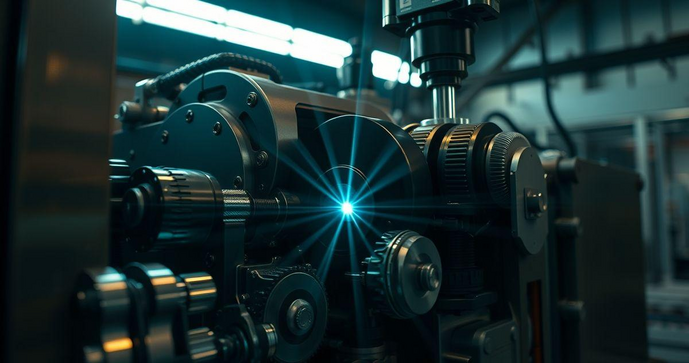
Por: Tiago - 23 de Fevereiro de 2025
O alinhamento a laser de eixos é uma técnica avançada que tem se tornado essencial na manutenção de máquinas industriais. Com a capacidade de garantir precisão e eficiência, essa metodologia reduz o desgaste de componentes e melhora o desempenho operacional. Neste artigo, exploraremos as vantagens, o funcionamento e os equipamentos necessários para implementar o alinhamento a laser de eixos, além de dicas de manutenção para maximizar seus benefícios.
Vantagens do Alinhamento a Laser de Eixos na Indústria
O alinhamento a laser de eixos é uma técnica que vem ganhando destaque na indústria devido às suas inúmeras vantagens. Essa metodologia não apenas melhora a eficiência operacional, mas também contribui para a longevidade dos equipamentos. A seguir, abordaremos as principais vantagens do alinhamento a laser de eixos e como ele pode impactar positivamente o desempenho das máquinas industriais.
Uma das principais vantagens do alinhamento a laser de eixos é a precisão que essa técnica oferece. Ao contrário dos métodos tradicionais, que podem ser suscetíveis a erros humanos e imprecisões, o alinhamento a laser utiliza tecnologia avançada para garantir que os eixos estejam perfeitamente alinhados. Isso resulta em uma redução significativa de vibrações e desgastes, prolongando a vida útil dos componentes e minimizando a necessidade de reparos frequentes.
Além da precisão, o alinhamento a laser também proporciona uma economia considerável de tempo. O processo de alinhamento tradicional pode ser demorado, exigindo várias medições e ajustes. Com o alinhamento a laser, as medições são feitas de forma rápida e eficiente, permitindo que as máquinas voltem a operar em menos tempo. Essa agilidade é especialmente importante em ambientes industriais, onde o tempo de inatividade pode resultar em perdas financeiras significativas.
Outro benefício importante do alinhamento a laser de eixos é a melhoria na eficiência energética. Quando os eixos estão desalinhados, as máquinas precisam trabalhar mais para compensar a falta de alinhamento, o que resulta em um aumento no consumo de energia. Com o alinhamento adequado, as máquinas operam de maneira mais eficiente, reduzindo o consumo de energia e, consequentemente, os custos operacionais. Essa eficiência energética não apenas beneficia a empresa financeiramente, mas também contribui para a sustentabilidade ambiental.
O alinhamento a laser também ajuda a minimizar o desgaste dos componentes. Quando os eixos estão desalinhados, há um aumento do atrito e do desgaste nas peças móveis, o que pode levar a falhas prematuras. Com o alinhamento correto, o desgaste é reduzido, o que significa que as peças duram mais e a necessidade de substituições frequentes é diminuída. Isso não apenas economiza dinheiro, mas também reduz o tempo e os recursos gastos em manutenção e reparos.
Além disso, o alinhamento a laser de eixos contribui para a segurança no ambiente de trabalho. Máquinas desalinhadas podem causar vibrações excessivas, que não apenas afetam o desempenho, mas também podem representar riscos para os operadores. Com o alinhamento adequado, as vibrações são minimizadas, criando um ambiente de trabalho mais seguro e confortável. Isso é especialmente importante em indústrias onde os trabalhadores estão expostos a máquinas pesadas e equipamentos em movimento.
Outro aspecto a ser considerado é a facilidade de uso dos sistemas de alinhamento a laser. A tecnologia atual permite que os operadores realizem o alinhamento de forma mais intuitiva, com interfaces amigáveis e instruções claras. Isso significa que menos treinamento é necessário, e os operadores podem realizar o alinhamento de maneira mais autônoma. Essa facilidade de uso é um grande atrativo para as empresas que buscam otimizar seus processos de manutenção.
O alinhamento a laser também é uma solução versátil, aplicável a uma ampla gama de equipamentos industriais. Desde motores e redutores até bombas e compressores, essa técnica pode ser utilizada em diversos contextos, tornando-se uma ferramenta valiosa para a manutenção industrial. Para garantir o funcionamento adequado de redutores, por exemplo, a Manutenção de redutores deve incluir o alinhamento a laser como parte do processo regular de manutenção.
Por fim, a implementação do alinhamento a laser de eixos pode resultar em um retorno sobre o investimento (ROI) significativo. Embora a tecnologia possa exigir um investimento inicial, os benefícios a longo prazo, como a redução de custos com manutenção, aumento da eficiência e prolongamento da vida útil dos equipamentos, superam amplamente os custos iniciais. As empresas que adotam essa tecnologia frequentemente relatam melhorias notáveis em seus processos operacionais e financeiras.
Em resumo, o alinhamento a laser de eixos oferece uma série de vantagens que podem transformar a maneira como as indústrias operam. Desde a precisão e eficiência até a segurança e economia de custos, essa técnica se destaca como uma solução essencial para a manutenção de máquinas industriais. Ao considerar a implementação do alinhamento a laser, as empresas podem não apenas melhorar seu desempenho, mas também garantir um ambiente de trabalho mais seguro e sustentável.
Como Funciona o Processo de Alinhamento a Laser
O processo de alinhamento a laser é uma técnica moderna e precisa utilizada na indústria para garantir que os eixos de máquinas e equipamentos estejam corretamente alinhados. Essa metodologia é fundamental para a manutenção de máquinas, pois um alinhamento inadequado pode levar a uma série de problemas, incluindo desgaste excessivo, aumento do consumo de energia e falhas mecânicas. Neste artigo, vamos explorar como funciona o processo de alinhamento a laser, suas etapas e a tecnologia envolvida.
O alinhamento a laser utiliza um sistema de feixes de luz laser para medir a posição dos eixos de uma máquina. O processo começa com a instalação de um dispositivo de alinhamento a laser, que consiste em um transmissor e um receptor. O transmissor emite um feixe de laser que é direcionado ao receptor, que está posicionado em um eixo adjacente. Essa configuração permite que o sistema meça a posição relativa dos eixos com alta precisão.
Uma das principais vantagens do alinhamento a laser é a sua capacidade de fornecer medições em tempo real. Isso significa que, à medida que o operador faz ajustes nos eixos, o sistema pode mostrar imediatamente as alterações na posição, permitindo que o alinhamento seja feito de forma rápida e eficiente. Essa capacidade de feedback instantâneo é uma das razões pelas quais o alinhamento a laser se tornou tão popular na indústria.
O primeiro passo no processo de alinhamento a laser é a preparação do equipamento. Isso envolve a limpeza das superfícies de contato dos eixos e a verificação de que não há obstruções que possam interferir nas medições. Uma vez que o equipamento está preparado, o transmissor é montado em um dos eixos, enquanto o receptor é posicionado no eixo adjacente. É importante garantir que ambos os dispositivos estejam firmemente fixados para evitar qualquer movimento durante o processo de medição.
Após a instalação dos dispositivos, o operador inicia o processo de medição. O transmissor emite um feixe de laser que é captado pelo receptor. O sistema calcula a diferença de altura e a desvio angular entre os eixos, fornecendo dados precisos sobre o alinhamento. Esses dados são exibidos em um display digital, permitindo que o operador visualize rapidamente a situação atual do alinhamento.
Com as medições em mãos, o próximo passo é realizar os ajustes necessários. O operador pode usar as informações fornecidas pelo sistema para determinar quais eixos precisam ser movidos e em que direção. O alinhamento a laser permite que esses ajustes sejam feitos com precisão, minimizando o risco de erros. Além disso, o sistema pode indicar a quantidade exata de movimento necessário para alcançar o alinhamento ideal.
Uma vez que os ajustes são feitos, o operador repete o processo de medição para verificar se o alinhamento foi alcançado. Essa etapa é crucial, pois garante que os eixos estejam agora corretamente alinhados. O alinhamento a laser é uma técnica iterativa, o que significa que pode ser necessário repetir o processo várias vezes até que o alinhamento perfeito seja alcançado. No entanto, a rapidez e a precisão do sistema a laser tornam esse processo muito mais eficiente do que os métodos tradicionais.
Além da precisão e eficiência, o alinhamento a laser também é menos suscetível a erros humanos. Os sistemas modernos de alinhamento a laser são projetados para serem intuitivos e fáceis de usar, permitindo que operadores com diferentes níveis de experiência realizem o alinhamento com sucesso. Isso é especialmente importante em ambientes industriais, onde a formação contínua dos funcionários pode ser um desafio.
Outro aspecto importante do alinhamento a laser é a sua versatilidade. Essa técnica pode ser aplicada a uma ampla gama de equipamentos, incluindo motores, redutores, bombas e compressores. Para garantir o funcionamento adequado de redutores, por exemplo, o Alinhamento a laser deve ser parte integrante do processo de manutenção regular.
Além disso, o alinhamento a laser pode ser realizado em diferentes condições de operação. Os sistemas de alinhamento a laser são projetados para funcionar em ambientes industriais desafiadores, onde vibrações e temperaturas extremas podem afetar o desempenho do equipamento. Isso significa que as empresas podem contar com essa tecnologia para manter seus equipamentos em funcionamento, independentemente das condições do ambiente.
Por fim, o alinhamento a laser não apenas melhora a eficiência operacional, mas também contribui para a segurança no ambiente de trabalho. Máquinas desalinhadas podem causar vibrações excessivas, que não apenas afetam o desempenho, mas também podem representar riscos para os operadores. Com o alinhamento adequado, as vibrações são minimizadas, criando um ambiente de trabalho mais seguro e confortável.
Em resumo, o processo de alinhamento a laser é uma técnica avançada que oferece precisão, eficiência e segurança na manutenção de máquinas industriais. Com a capacidade de fornecer medições em tempo real e a facilidade de uso, o alinhamento a laser se destaca como uma solução essencial para garantir o desempenho ideal dos equipamentos. Ao considerar a implementação do alinhamento a laser, as empresas podem não apenas melhorar seu desempenho, mas também garantir um ambiente de trabalho mais seguro e sustentável.
Equipamentos Necessários para Alinhamento a Laser de Eixos
O alinhamento a laser de eixos é uma técnica essencial para garantir a eficiência e a durabilidade de máquinas industriais. Para realizar esse processo de forma eficaz, é necessário utilizar equipamentos específicos que garantam medições precisas e ajustes adequados. Neste artigo, vamos explorar os principais equipamentos necessários para o alinhamento a laser de eixos e como cada um deles contribui para o sucesso do processo.
O primeiro e mais importante equipamento para o alinhamento a laser é o sistema de alinhamento a laser em si. Este sistema geralmente consiste em um transmissor e um receptor. O transmissor emite um feixe de laser que é direcionado ao receptor, que está posicionado em um eixo adjacente. Essa configuração permite que o sistema meça a posição relativa dos eixos com alta precisão. Existem diferentes modelos de sistemas de alinhamento a laser disponíveis no mercado, variando em complexidade e funcionalidades. Alguns modelos mais avançados oferecem recursos adicionais, como conectividade Bluetooth e software de análise, que facilitam a interpretação dos dados coletados.
Além do sistema de alinhamento a laser, é fundamental ter um suporte adequado para o transmissor e o receptor. Esses suportes garantem que os dispositivos estejam firmemente fixados e alinhados durante o processo de medição. Um suporte instável pode resultar em medições imprecisas, comprometendo todo o processo de alinhamento. Os suportes podem ser ajustáveis, permitindo que os operadores posicionem os dispositivos de forma ideal, independentemente do espaço disponível ao redor da máquina.
Outro equipamento importante é o nível de bolha ou um nível eletrônico. Esses instrumentos são utilizados para garantir que o transmissor e o receptor estejam perfeitamente nivelados antes de iniciar o processo de medição. Um alinhamento incorreto pode levar a erros nas medições, resultando em um alinhamento inadequado. Portanto, é essencial verificar o nível de cada dispositivo antes de começar a coleta de dados.
Além disso, é recomendável ter um conjunto de ferramentas básicas à disposição. Isso inclui chaves de fenda, chaves inglesas e alicates, que podem ser necessários para realizar ajustes nos eixos durante o processo de alinhamento. Ter as ferramentas certas à mão facilita a realização de ajustes rápidos e eficientes, economizando tempo e esforço durante o processo.
Outro equipamento que pode ser útil é um computador ou tablet com software de alinhamento. Muitos sistemas de alinhamento a laser modernos vêm com software que permite a análise detalhada dos dados coletados. Esse software pode gerar relatórios, gráficos e recomendações para ajustes, facilitando a interpretação dos resultados e a tomada de decisões. A utilização de tecnologia para análise de dados é uma tendência crescente na indústria, e o alinhamento a laser não é exceção.
Além dos equipamentos mencionados, é importante considerar a utilização de dispositivos de segurança. O alinhamento a laser envolve o uso de feixes de luz que podem ser prejudiciais aos olhos se não forem manuseados corretamente. Portanto, é recomendável que os operadores utilizem óculos de proteção adequados durante o processo. Além disso, é importante garantir que a área ao redor da máquina esteja livre de obstruções e que todos os operadores estejam cientes do processo em andamento.
Para garantir o funcionamento adequado de redutores, por exemplo, a Manutenção de redutores industriais deve incluir o alinhamento a laser como parte do processo regular de manutenção. Isso não apenas melhora a eficiência dos redutores, mas também prolonga sua vida útil, reduzindo a necessidade de reparos frequentes.
Outro aspecto a ser considerado é a calibração dos equipamentos. Antes de iniciar o processo de alinhamento, é importante garantir que o sistema de alinhamento a laser esteja devidamente calibrado. A calibração deve ser realizada de acordo com as instruções do fabricante e pode incluir a verificação de pontos de referência e a realização de testes de precisão. Um sistema calibrado garante medições mais precisas e confiáveis, resultando em um alinhamento mais eficaz.
Por fim, é importante mencionar que a formação e o treinamento dos operadores são fundamentais para o sucesso do alinhamento a laser. Embora os equipamentos sejam projetados para serem intuitivos e fáceis de usar, a experiência e o conhecimento dos operadores podem fazer uma grande diferença na qualidade do alinhamento. Investir em treinamento adequado garante que os operadores estejam familiarizados com os equipamentos e as melhores práticas, resultando em um processo de alinhamento mais eficiente e eficaz.
Em resumo, o alinhamento a laser de eixos requer uma série de equipamentos específicos para garantir medições precisas e ajustes adequados. Desde o sistema de alinhamento a laser até suportes, níveis, ferramentas básicas e software de análise, cada um desses equipamentos desempenha um papel crucial no processo. Além disso, a segurança, a calibração e a formação dos operadores são aspectos que não podem ser negligenciados. Com os equipamentos certos e o conhecimento adequado, as empresas podem garantir que seus processos de alinhamento sejam realizados de forma eficiente, resultando em máquinas mais duráveis e eficientes.
Manutenção e Cuidados Após o Alinhamento a Laser
Após a realização do alinhamento a laser de eixos, é fundamental implementar uma rotina de manutenção e cuidados para garantir que os benefícios obtidos sejam mantidos ao longo do tempo. O alinhamento adequado não é um evento isolado, mas parte de um processo contínuo que envolve monitoramento, ajustes e manutenção regular. Neste artigo, discutiremos as melhores práticas de manutenção e cuidados que devem ser adotados após o alinhamento a laser.
Uma das primeiras ações a serem tomadas após o alinhamento a laser é a verificação do alinhamento periodicamente. Embora o alinhamento a laser ofereça resultados precisos, fatores como vibrações, mudanças de temperatura e desgaste natural dos componentes podem afetar o alinhamento ao longo do tempo. Portanto, é recomendável realizar medições regulares para garantir que os eixos permaneçam alinhados. A frequência dessas medições pode variar dependendo do tipo de equipamento e das condições de operação, mas uma verificação trimestral é uma boa prática para a maioria das aplicações industriais.
Além das medições regulares, é importante monitorar o desempenho das máquinas. Fique atento a sinais de problemas, como vibrações excessivas, ruídos anormais ou aumento no consumo de energia. Esses sintomas podem indicar que o alinhamento foi comprometido ou que há outros problemas mecânicos em jogo. Se qualquer um desses sinais for identificado, é essencial investigar a causa e, se necessário, realizar um novo alinhamento a laser.
A lubrificação adequada dos componentes também é um aspecto crucial da manutenção após o alinhamento a laser. A falta de lubrificação pode levar ao desgaste prematuro dos eixos e outros componentes, comprometendo o alinhamento e a eficiência das máquinas. Certifique-se de seguir as recomendações do fabricante em relação à frequência e ao tipo de lubrificante a ser utilizado. A lubrificação deve ser realizada em intervalos regulares e sempre que forem feitas manutenções nos equipamentos.
Outro cuidado importante é a limpeza das superfícies de contato dos eixos. Poeira, sujeira e detritos podem se acumular nas superfícies de contato, interferindo no alinhamento e causando desgaste. Realize limpezas regulares para garantir que as superfícies estejam sempre em boas condições. Utilize produtos de limpeza adequados e evite o uso de solventes que possam danificar os componentes. A limpeza deve ser parte integrante da rotina de manutenção, especialmente em ambientes industriais onde a sujeira é comum.
Além disso, é essencial verificar as condições dos suportes e fixações dos eixos. Com o tempo, os parafusos e suportes podem se soltar devido a vibrações e movimentos. Realize inspeções regulares para garantir que todos os componentes estejam firmemente fixados. Se necessário, aperte os parafusos e faça ajustes para evitar que o alinhamento seja comprometido. Um suporte instável pode levar a medições imprecisas e a um alinhamento inadequado, resultando em problemas operacionais.
Para garantir o funcionamento adequado de redutores, por exemplo, a Manutenção de redutores de velocidade deve incluir a verificação do alinhamento e a lubrificação regular. Isso não apenas melhora a eficiência dos redutores, mas também prolonga sua vida útil, reduzindo a necessidade de reparos frequentes.
Outro aspecto a ser considerado é a documentação do processo de alinhamento e das manutenções realizadas. Manter registros detalhados das medições de alinhamento, ajustes feitos e manutenções realizadas é fundamental para monitorar o desempenho ao longo do tempo. Esses registros podem ajudar a identificar padrões e a prever quando novas manutenções ou alinhamentos podem ser necessários. Além disso, a documentação pode ser útil para auditorias e para garantir a conformidade com as normas de segurança e qualidade.
É importante também treinar os operadores e a equipe de manutenção sobre a importância do alinhamento e dos cuidados necessários após o processo. A conscientização sobre os sinais de problemas e a importância da manutenção regular pode ajudar a prevenir falhas e a garantir que as máquinas operem de forma eficiente. Investir em treinamento contínuo é uma prática recomendada que pode trazer benefícios significativos a longo prazo.
Por fim, considere a possibilidade de implementar um programa de manutenção preditiva. Esse tipo de programa utiliza tecnologias avançadas, como sensores e monitoramento em tempo real, para prever quando as máquinas podem precisar de manutenção. Isso permite que as empresas realizem manutenções antes que os problemas se tornem críticos, minimizando o tempo de inatividade e os custos associados a reparos emergenciais.
Em resumo, a manutenção e os cuidados após o alinhamento a laser são essenciais para garantir que os benefícios do alinhamento sejam mantidos ao longo do tempo. Realizar medições regulares, monitorar o desempenho, lubrificar os componentes, limpar as superfícies de contato e verificar as condições dos suportes são práticas fundamentais. Além disso, manter registros detalhados, treinar a equipe e considerar a implementação de um programa de manutenção preditiva são passos importantes para garantir a eficiência e a durabilidade das máquinas industriais. Com uma abordagem proativa em relação à manutenção, as empresas podem maximizar o desempenho de seus equipamentos e reduzir custos operacionais a longo prazo.
Em conclusão, o alinhamento a laser de eixos se destaca como uma solução indispensável para a manutenção eficaz de máquinas industriais. Ao garantir precisão e eficiência, essa técnica não apenas prolonga a vida útil dos componentes, mas também otimiza o desempenho operacional das máquinas. A compreensão das vantagens, do funcionamento e dos equipamentos necessários para o alinhamento a laser, juntamente com a implementação de práticas de manutenção adequadas, é fundamental para maximizar os benefícios dessa metodologia. Com um alinhamento adequado, as empresas podem reduzir custos operacionais, minimizar o tempo de inatividade e criar um ambiente de trabalho mais seguro e produtivo.